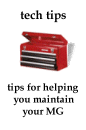

Chicagoland MG Club
Tech Tips
General Tips
MGA Tips
MGB Tips
Midget Tips
MGT's Tips
MMM Tips
Tech Session Photo Archives
|
|

MG T-Series
How To Do A Complete Engine Tune-Up
Part I
by Skip Burns
March 2000
There is ample anecdotal evidence that when an XPAG engine starts to run rough or give trouble, the first thing the amateur mechanic does is reach for a wrench (hammer?) and head for the carburetors. This is a serious mistake. SU carburetors, having only three moving parts, are extremely reliable. When SU’s do re-quire adjustment, it’s usually result of somebody having fiddled with them. Unlike most other carburetors, once SU’s are properly tuned they should stay that way for a long time. Moreover, unlike no other carburetor, when the initial tuning is complete the SU design permits further fine-tuning and confirmation of the results. Engine problems, when they occur, mostly lie elsewhere —with compression (leaky rings, intake or exhaust valves, or head gaskets), or some-where within the ignition system (including timing). No amount of fiddling with the carbs will help an engine with these problems. For these reasons, this and another paper are devoted to covering all aspects of engine tune-up, starting with compression checks and ending with adjusting the carburetors.
What follows is a recap of a recent tech session held in my garage and devoted to covering several aspects of tuning up XPxx engines; i.e., engines installed in all T-series cars, except for the TA. Because many tune-up principles applicable to T-cars are also applicable to other MG models, reference to this document can help owners interested in knowing more about their cars and how to keep them tuned. Owing to its complexity, the topic is divided into two, separate papers. The first (Part I) covers the essentials of compression, rocker clearances, ignition and timing, and the checks that must be made before tuning the carbs. A second paper (Part II) covers the ins and outs of tuning SU carburetors while, at the same time, dispeling some of the myths about them.
Both papers are presented in outline form for easy referral when doing a tune-up. Sub-text is added only where necessary for clarification or a discussion of theory. Source material is provided at the conclusion of Part II.
Note: The experienced mechanic may find this dull and boring, but please keep in mind that the primary intent is to help the novice mechanic.
Cheers and happy motoring,
Skip Burns (1939 MG TB 0304) Aristarcus@aol.com
229 Alcalde Moreno, Hollywood Park, Texas 78232
|
|
Tools
Rule #1. Having the right tools handy is absolutely necessary for successful engine tuning. Clear your workbench of extraneous materials and neatly lay out the following tools.
* Standard screwdrivers both short and long.
* Spark plug wrench and tester.
* Whitworth/BS wrenches to adjust carburetor jets and loosen the distributor locking nut.
* Compression tester.
* Uni-Synch (to balance the airflow between dual carbs).
* Engine Test & Diagnostic Meter (dwell, rpms, points, ohms, voltages and more). No backyard mechanic should be without one of these. If you want to know what’s going on in your engine, get one. A relatively inexpensive item.
* A Colortune (Yes! (used to set the timing.)
* Feeler gauges.
* Pince-nosed pliers (to remove the cotter pins holding the jet/choke levers).
* Jet centering tool.
* ¼-inch socket driver (to loosen the nuts on the spindle clamp connecting the throttles).
* Strobe light for cars with vacuum advance (not covered in these articles).
* Carb rebuild kit (for those going whole hog).
* Pencil and paper to record readings.
* New rocker arm cover gasket.
* A crank to turn the engine (not absolutely required).
* A 7-inch length of piano or hanger wire
* New cotter pins (to replace those removed from the choke and jet levers).
* An assistant to help during compression tests (“Hey, honey, can you come out here for a minute?”)
Rule #2. Clear off a separate, uncluttered space on your workbench for parts. Keep everything scrupulously clean.
Compression
Rule #3. The greatest potential for a good running engine is its ability to develop high, equal pressure in all cylinders.
Problem Areas: leakage past rings, inlet and exhaust valves and the head gasket;
Faulty Rings: high oil consumption and/or fouled plugs/low power;
Faulty Valves: Incomplete filling and scavenging of cylinders/burned valves/low power;
Faulty Head Gasket: Low power, rough running, poor fuel economy, or worse.
Adjusting the Valves
Rule #4. It’s my belief that the more an MG owner knows about the inner workings and hidden mechanisms of his car’s engine, the easier time he or she will have keeping it tuned and running properly.
A text insertion here explains the intricacies of the valve train, importance of proper valve clearance and why you should check valve train clearances before doing a compression check.
The valve train is something akin to the anklebone connected to the knee bone, the knee bone connected to hipbone affair. The camshaft down in the bowels of the engine has eight lobes plus three gears. One gear is connected to the timing chain. Another powers the oil pump and yet another turns the distributor camshaft. Riding on the lobes are eight tappets (or lifters) and atop these are eight pushrods. The pushrods have cupped tops which accept domed heads located on the ends of the rocker arms. At the opposite end (the valve end) of the rocker arm, the end is flat and rides just above the top of the valve when it’s closed (sticking up). The valve is forced up and closed by springs wound in opposite directions to prevent their interfering with each other. When the push rod on the opposite end of the rocker arm rises, the rocker arm rotates and pushes down on the valve stem, compressing the spring and opening the valve (pushing it down and away from the seat in the head).
A certain amount of free play, or valve lash as it’s sometimes called, is needed to allow for differences in the expansion rate of the various parts, plus wear and tear. After initial adjustment, it’s usually wear and tear that necessitates re-adjustment of the valve lash, for it must be set precisely to account for erosion of the various parts. A final objective is to make sure the valves seat properly when closed. The valve end of the rocker arm must not touch the end of the valve stem when the valve is closed. The space between them is a mere .012 or .019 inches, depending on the series car you own. It’s this clearance that must be checked and adjusted as needed.
When hot gases are exhausted through an open valve, it becomes extremely hot. The exhaust and all the thrashings about going on under the hood are generating that heat. At 50 mph, the valves are opening and closing 25 times/second, resulting in considerable heat buildup. In the course of the complete cycle, the valves are closed about 66 percent of the time and open about 33 percent of the time. This is important, because when the valve seats, the seat itself acts as a heat sink, transferring some of the heat away from the valve. Should the valve remain open even a tiny bit, the extreme temperature (1400 degrees Fahrenheit) of the exhaust gas can melt the valve and possibly ruin the seat, necessitating a valve job. With a leaky valve, the engine will suffer a loss of power. Therefore, it’s absolutely critical that the free play in the valve train not only compensate for expansion, wear and tear, but also allows the valve to seat properly. Because you want these clearances to be spot on when driving the car (hot), they must be adjusted when the engine is hot. They cannot be set cold. You can test this by doing a proper hot adjustment of the valves and letting the engine cool. Check the clearances when the engine is cool and you’ll find not only are they different from one another, they’re far from the .019-inch settings called for when the engine is hot. This accounts for the clattering noise when starting a cold engine. With properly adjusted valves, much of this noise disappears as the engine warms up. MG engines are famous for this sound.
Adjusting the valves before the compression check
- Remove the air cleaner and ducting (do this after driving the car and the engine will cool down before you finish getting the stuff off).
- Drive the car for thirty minutes or until the engine reaches operating temperature.
- Return to your garage and remove the rocker arm cover.
Measuring tools required: dial indicators are more precise, but they’re expensive. Stick to feeler gauges and use the Go-No-Go method. Why? Because what feels like .019 inches of clearance to you may feel like .018 or .020 inches to someone else. The Go-No-Go method eliminates all arguments.
Measuring the clearance
- TB/TC/TD MK II to engine number 24115 = .019 inches
- TD/TD MK II from engine number 24116 = .012 inches
- TF/TF 1500 = .012 inches
- Measured on the valve side of the rocker arm.
- If you’re not sure which type of head you have, use the .019-inch clearance.
Note: These clearances are for the original camshafts. After many years and many rebuilds, your engine may no longer have the original cam. Fitting one of the later cams during a rebuild was (is?) a common practice. Various after market proprietary cams, such as Crane or Iskendarian, require different clearances. Don’t blindly use a clearance just because of the engine number. Somewhere I have an article on how to determine what cam you have. If I can find it, it will be included at the conclusion of Part II.)
- Have three feeler gauges ready: .018-, .019- and .020-inch.
- Turn the crank until the #1 valve is fully closed (See below).
- Slack off adjusting nut from screw on push-rod side of engine using a 1/4-inch Whitworth or 5/16-inch British Standard (BS) wrench.
- Insert the .019-inch feeler gauge on the valve side between the valve end and rocker arm foot.
- Turn adjusting screw until blade is just trapped and tighten the nut.
- Check clearance using the Go-No-Go method.
- Insert the .018 feeler gauge. It should feel loose.
- Insert the .020 feeler gauge. It should feel tight or not go in at all.
- Insert the .019 feeler gauge. It should still feel just right.
- If the adjustment fails, do it again.
- Repeat for remaining seven valves (see below).
System of Nines. Determining when a valve is fully closed (the point where it is adjusted) is difficult because of the broad, round shape of the bottom part of the cam lobe that lifts or lowers the tappets and pushrods. However, it is easy to see when a valve is open because of the rapid rise of an open valve (sharp rise on cam lobe). Fortunately, MG designed the engine so that when one valve is open (easy to see), another is closed. This leads to the System of Nines. Looking at the rocker arms and counting from the front of the engine (the most forward rocker arm being #1):
With This Open Adjust This
#8 #1
#6 #3
#4 #5
#7 #2
#1 #8
#3 #6
#5 #4
#2 #7
When finished, replace the rocker arm cover.
- If the old gasket is good, replace cover using original grooves in gasket.
- If gasket is torn, replace with a new gasket after scraping the old one off, being careful not to let any small pieces drop onto the head where they may enter the oil galleries.
- If possible, replace with a Nitrile gasket (better than cork).
Leave air cleaner and ducting off—for later carburetor tuning.
Compression Check (Step 1)
Remove all spark plugs.
Have pencil and paper ready to record readings.
Have assistant standing by (“Honey, it’s time!”)
Connect compression gauge to #1 cylinder.
Have assistant crank engine (ignition switch—off) through six compression stokes with the throttle wide open.
* Needle should jump six times.
Record the highest reading.
Repeat on other cylinders.
Interpretation of Readings (Step 2)
The MG factory never published pressure readings for compression checks. However, experience over the years has shown the following to be close enough:
Series Max.psi Min.psi Max.psi variation
TB/TC/TD 140 100 20
TD Mk II/TF 150 110 20
Note: if the compression ratio (directly related to compression pressure) has been raised, e.g., by skimming the head, pressures will be higher.
If needle jumps to nearly highest reading, then climbs in smaller jumps; good news: that cylinder passes the compression check.
If gauge reads low on first stroke and builds slowly never reaching the minimum psi: bad news; that cylinder fails the compression test. The rings are probably bad.
- Confirm by conducting a wet test.
- Squirt a tbs. of motor oil into the cylinder.
- Crank engine a few times to spread oil.
- Conduct another compression test.
- Higher reading confirms bad rings. Overhaul of the engine is required. Don’t apply quick cure using STP or any other wonder additive. Modern detergent oils have eliminated problems with gummed up rings.
- No difference in readings: problem with a valve or head gasket.
- Any problems found during the compression check must be fixed before tuning carbs.
Ignition System
Continuing under Rule #4 — nothing so baffles the backyard mechanic than the ignition system. He or she generally knows what it’s supposed to do, but is often mystified about how it does it. In fact, the system is quite simple, almost crude in fact, but the job it performs is extremely exacting. It consists of the coil, distributor, high and low-tension wiring, a condenser, spark plugs and two switches—the ignition switch and the points. The only precision parts are situated inside the distributor; i.e., the camshaft, the cam itself and the points. Otherwise, it’s basic electricity 101.
A measure of the precision of the ignition system can be gleaned from the fact that at 3,000 RPM, it produces 100 sparks/second. And these sparks must be timed to an accuracy measured in thousandths of a second. Unquestionably, this calls for a high degree of precision in the manufacture and maintenance of the system.
The heart of the system relies on two basic principles of electricity: 1) when a wire is wound around a soft iron core and a voltage is induced in it, a magnetic field (flux) is set up in and around the iron core; 2) when the field surrounding an iron core collapses, a voltage will be produced in any wire that’s within the field. This is the very essence of the coils in our ignition systems.
The coil itself is made up of primary and secondary wire windings. The primary wire is the low voltage (12 volt) wire and the secondary wire is the high voltage (up to 30,000 volts) wire. The primary wire is routed from the battery through the ignition switch to the coil and on to the points which, in turn, are connected to ground. Thus, anytime the points are closed electricity flows through the primary wire and a magnetic field is induced in the iron core of the coil. At this point, nothing has happened except that 12 volts are flowing through the coil and points to ground. When the points open, the electricity flowing into the coil stops and the magnetic field collapses. Recalling the second of our electrical principles, a voltage is now induced in the secondary windings. How much voltage? The coil is actually a small transformer. The primary (12 volt) windings are relatively thick wire wound only a hundred or so times around the outer wall of the coil. The secondary winding is made up of very thin wire wound thousands of times close to and around the central core. In fact, a coil can have has much as a mile of secondary winding inside of it. Because there is so much more secondary than primary wiring in the magnetic field, when it collapses, a large rise in voltage occurs—as high as 30,000 volts. This high voltage is delivered to the top of the distributor, whence it travels to the rotor, jumps the gap to the stub and goes to the spark plug.
When the points close again, the primary field rebuilds, magnetizes the iron bar, and awaits the opening of the points when the whole process restarts—all of this at rates of up to 200 times a second. There’s an awful lot of sparkin’ goin’ on down there!
There is nothing particularly ingenious about the system, as the principles governing it have been known for more than a century. What is clever, however, is the arrangement of the distributor camshaft and cam. The engine manufacturer must design the valve train, distributor shaft and the cam to exacting specifications: the cam must be timed to open the points at the precise moment the any piston reaches TDC at the beginning of its power stroke.
What about the condenser? The input to the condenser is the same primary voltage that’s fed to the points. A problem arises when the points open (when we think we see the points opening, they’ve already been open for some time). The residual voltage across the points generates an arc. This arc causes pitting of the points, increasing their resis-tance. When that happens, the points must be replaced. The condenser’s job is to reduce or eliminate arcing across the points. Here’s how it does it. The condenser is in parallel with the points, with 12 volts going in one end and the other connected to ground. But it’s also a capacitor, which means it has a some internal resistance; moreover, because it’s a capacitor, it can store and release energy it. No voltage flows across it during the build-up of the magnetic field, because the primary voltage seeks the easiest path to ground—across the points—not the condenser. But when the points first open, the voltage bounces back to the capacitor seeking the more difficult path to ground (instead of arcing across the points). But finding no ground, it gets stored, then ricocheted back up the line to the primary windings where it enhances the collapse of the field, further increasing the voltage output to the secondary winding.
The sloppiest part of the system is the rotor, and for good reason. Have you ever noticed, when replacing the rotor, that it can be wobbled left and right a few degrees? And what about the funny shape of the top, like the thumb of a left-handed hitchhiker trying to catch a ride. First, the rotor has nothing to do with the timing of the high voltage arc. Only the camshaft, cam and the points control timing. The rotor could care less when the voltage arrives. It just sits there twiddling its thumb in circles waiting for something to happen. When it does, the camshaft makes sure the rotor is in the right position—that is, next to the correct high-tension stub inside the distributor cap. When the timing is at Top Dead Center, the cam on the cam shaft opens the points and a voltage arc crosses to the stub from the pointy of the thumb. Why from the pointy end?
You’ll remember from an earlier article in the Newsletter that the maximum degree of advance of our engines is 30 degrees before TDC. You’ll also recall from the same article why we advance the firing of the plugs ahead of TDC when accelerating the engine. Right. If the distributor is advanced say, 30 degrees, the outer casing, points and stubs—everything in it except the rotor and shaft is moved 30 degrees clockwise. Now, it just happens that the thumb on the rotor is slightly longer than a 30-degree arc around the inside of the distributor. This allows the arc to jump across further back on the thumb –closer to the big knuckle. In case you’re wondering, the few extra degrees of length in the thumb allow for retardation, too. In sum, the long thumb of the rotor allows the spark to jump regardless of the amount of advance or retardation. Hey, this is beginning to make sense!
Now that we have full comprehension of the ignition system, let’s get on with the checks.
Ignition System Checks
Spark plugs:
- Operate in an extremely hostile environment, so must be looked after frequently.
- Clean, file and gap (.025 inches for all T-series cars)
- The spark that jumps across the plug gap likes to see sharp, square corners. In the old days, the negative terminal used to be round. It didn’t take long before they discovered that square corners work better. Gently file the negative terminal clean of all debris and square it away. If necessary, widen the gap so you can get a file on the underside and on top of the positive terminal. Then, regap it.
- Purchase from a reliable, internationally known manufacturer; e.g. Champion, AC, Autolite/KLG, Bosch and NGK. NAPA stores carry all of these and more.
- Type: 14 mm with a ½-inch or ¾-inch reach. A word of caution here. Make sure you know the correct reach for your head. There’s a number embossed on the top, forward right side of the head. Any head stamped with the number 22592 takes a ½-inch plug. Later heads had different numbers and, as far as I know, they all take ¾-inch plugs. If you’re not sure, make a small bend in the tip of a wire. Reach down into the plughole and measure it. Never, never put the wrong plug into the wrong head!
- Heat range: plugs are designed to operate in a narrow heat range. A colder plug dissipates heat faster than a hotter one, and vice versa.
- A higher number on the plug indicates a hotter plug, except for NGK, where it indicates a colder plug. (I called NGK and asked why, but they couldn’t explain it.)
- Recommendation: NGK B6HS (hotter) or B7HS (colder):
- How to know which to buy? It depends on your driving conditions. If you drive at highway speeds on the freeway like I do, you’ll want a hotter plug. If you limit your driving to tooling around the local neighborhood, a colder plug is called for. Experimentation is the best solution here. I use ½-inch reach NGK B6HS plugs and have had good results.
- What to look for when examining a plug. Plugs should have a light tan or gray color around the terminals and on the inner insulator. A dry, sooty look means your carbs are probably set too rich. A wet, sooty look most likely indicates bad rings.
- Distributor Cap and H.T Cables: Clean, check for cracks and, if there are any, replace the cap or cables.
- Points: clean, file or stone smooth. The manual says the gap should be between .010 and 012. Forget the small stuff. Set the gap at .011.
Again, because of differences in interpreting feeler gauge widths, the best bet is to use a dwell meter to set the gap. Before getting your feeler up, you’ve got a problem. You must know the type of cam lodged in your distributor. Lucas manufactured three types of distributors for T-Type cars, all of them interchangeable, including their cams. Your manual may say you have one type of distributor, but a previous owner may have substituted another. You could check the numbers on the side of the distributor. Those which have either of the letters A – D following the number indicate installation of a symmetric or asymmetric cam. Later models had an E suffix, indicating installation of a high lift cam. The problem is, you can’t read the number or letter without removing the distributor. Another way is to check you manual, but caution is advised as the distributor may have been changed out.
T-series cars up to TD/24489 (suffixes A-D) had either symmetric or asymmetric cams. Later series cars used high lift cams (suffix E).
The only sure way to know whether you have a symmetric, asymmetric or high lift cam is to look at it. Remove the cover from the distributor and take off the rotor. Get some good lighting behind you so you can see the cam clearly. While my descriptive skills leave much to be desired, I believe if you compare what follows with what you’re looking at, you’ll immediately recognize which type of cam you have. This is important because the gap settings/dwell angles differ for each type of cam.
Symmetric Cam: Rounded corners with absolutely straight sides. This is the type of cam I have in my TB.
Asymmetric Cam: Same rounded corners, but the sides bulge a little; to wit, they are not straight as in the symmetric cam.
High Lift Cam: Sharp, high-lift corners with the bulging sides as in the asymmetric cam.
If you have difficulty identifying your cam, bring your car by and I’ll have a look at it.
- Point Gaps/Dwell Settings
Symmetric Asymmetric High Lift
Gap: .010-.012 .010-.012 .014-.016
Dwell Angle: 41-49 45-53 57-63
Regarding dwell angles, shoot for the middle figure, i.e., 45 degrees for the symmetric, 49 degrees for the asymmetric and 60 degrees for the high lift. As a measure of how small these differences are, note that the gaps for the symmetric and asymmetric cams are the same, but the dwell angle is different. That’s because using a feeler gauge, you can’t tell the difference between .011 and something approaching .012 when setting a gap. Surely, that’s sufficient justification for owning a dwell meter.
Ignition Timing
By now, you should have a fair understanding of ignition timing and the need for precision. Earlier, we covered the sequence of events leading up to ignition. It may be helpful here to take a moment and review what happens after ignition, if only to reinforce the notion of how critical ignition timing is.
Most engines fire their plugs at or very near Top Dead Center (TDC) when the engine is idling. Of course, we know now that as the engine speeds up, the ignition point must be advanced to allow full burning of the fuel/air mixture at the same point of maximum push on the piston. Following ignition, a flame front (not an explosion) proceeds across the top of the piston igniting the fuel. At some point, the fuel is completely burned. This is the point of maximum push. The air has become fully heated. With space in the cylinder expanding as the piston descends, the air begins to cool. Some time before reaching Bottom Dead Center (BDC), the exhaust valve opens. The fuel has done its job and now needs to be pushed out of the cylinder. As the piston passes BDC, it begins to rise and force the burned mixture out through the open exhaust valve. Just before reaching TDC, the intake valve opens. The piston passes TDC and begins to draw in a new mix of fuel and air. Shortly after TDC, the exhaust valve closes, sealing the cylinder except for the inlet valve. The piston continues down, drawing in more fuel and air. Shortly after passing BDC, the inlet valve closes and the rising piston begins compressing the gas. When it reaches TDC, the gas is ignited by the spark plug and the whole process starts over again. Not only is the importance of precise timing obvious, the need for having tight valves is also evident.
The amazing thing is that this sequence of events can occur at rates up to and as high as 400 times a second.
Before setting the timing to TDC, there’s one more thing. On T-Cars, it’s not possible to set the timing using a strobe light (dynamic timing). Here’s why. The timing must be set when the idle speed is as low as possible, i.e., just ticking over (700-800 RPM). The problem is, the advance weights in our distributors beginning advancing the ignition at around 300-RPM. By the time the car is ticking over at 700 RPM, the timing has automatically advanced 4 to 5 degrees before TDC. This necessitates static timing.
Checking and Statically Adjusting the Timing
Remove all the spark plugs.
Use a crank or pull on the fan belt to get the number one cylinder close to TDC.
- The easy way to do this is to take the cap off the distributor and observe the position of the rotor. When the rotor is at or near the stub for the number one cylinder, the piston will be close to TDC on its compression cycle.
- Adjust (pull on the fan belt) the fan pulley so the mark on the pulley lines up exactly with the arrow marker located on the front of the timing chain cover. When lined up, the piston in the number one cylinder is precisely at TDC.
Replace the distributor cap and install the Colortune in the number one cylinder plug hole. Connect the high tension (HT) wire coming from the distributor to the top of the Colortune. Make sure you get the correct wire.
Note: The Colortune is nothing more than a spark plug that allows you to see the spark or flame inside the cylinder. Observations are made by looking at the ring of glass that surrounds the top of the plug.
Loosen the nut and bolt that locks the distributor in place—not the one down on the block—the one just under the distributor. Loosen just enough to allow rotation of the distributor.
Grasp the distributor and rotate 10 or 15 degrees counter-clockwise to the left. By doing this, you are retarding the timing.
Turn on the ignition switch.
Grasp the distributor and slowly, very slowly begin rotating it to the right, clockwise. You are now advancing the timing. Keep your eye on the Colortune. When you see a flash, you’ve reached TDC ignition. It may startle you, so repeat the process several times to get the distributor in precisely the correct position.
Carefully, so as not to disturb the position of the distributor, tighten the locking nut.
Congratulations. You’ve just set your ignition timing to Top Dead Center. Things are looking up. Only the carburetors need tuning to finish the job.
Here’s a tech tip. When our cars were originally manufactured, the fuel used in Britain was a cheap fuel with an octane rating of around 70. It was called Pool gas. With that octane rating, the wonder is that they got it to burn at all. Nowadays, we have octane ratings running from 86 to 92. Because of improvements made in the fuel quality and octane ratings, some owners have re-adjusted their timing to 5 or even 10 degrees BTDC. The idea is to obtain more power through better timing. Because we have no marks for these settings, some people say it cannot be done with any accuracy. Rubbish! All it takes is a little math. A word of caution: you will know when you’ve gone too far if the engine knocks or pings with the new setting. That’s when it’s time to back off. If you hear no knocking, you should get more power out of the engine. This is something to play with on a lazy Saturday afternoon.
Adjusting the Static Advance To 5º or 10º Before TDC
The diameter of the crank pulley is 95mm or 3.74 inches.
Multiply that by the magic Greek pi (? = 3.1416) and you get 11.75 inches, the circumference of the pulley.
5º is 1/72 of 360 degrees.
11.75 ? 72 = 0.163 inches.
Standing in front of the engine and facing aft, make a mark on the pulley 0.163 inches to the right of the original timing mark. Use a file or mark with paint. The distance is roughly equal to the height of three stacked dimes. Making the mark to the right of the original TDC mark advances the timing.
Readjust (statically) the timing to the new mark.
Double the distance for 10º advance.
That’s it for now. In Part II, I’ll provide some tips on tuning the SU carbs. Remember, the purpose of everything we’ve done so far is to prepare the engine for carburetor tuning.
Cheers, Skip
Back to MGT Tech Tips
|
|

©2002 Chicagoland MG Club, All rights reserved.
|