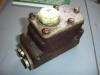 Master Cylinder 7/8" bore with locked up pistons. Getting ready to get rebuilt. |
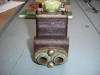 Front view |
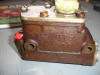 Side view |
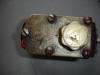 Noticed immediately that cap had crack in it. |
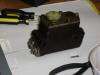 I would suggest getting a thick piece of cardboard with smooth surface so any fluids can be wiped up and not soaked in. |
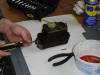 Unscrew two screws on front plate. If there was rubber caps, take off and discard. |
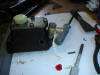 TRICK OF THE TRADE for seized pistons - place banjo bolt, banjo and adapter in one of the holes. |
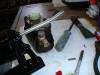 Ensure banjo bolt and adapter is tight, take grease fitting off and screw in rod from grease gun into the banjo. |
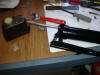 Fill master cylinder reservoir with fluid. |
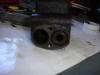 Pump grease gun and watch the locked up piston come out. |
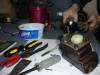 Continue to pump until piston is sticking out enough to grab hold of. Be careful because it is being moved out with pressure and could cause injury. |
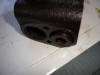 If piston shoots out, keep clear. |
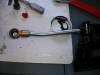 Once piston is far enough out to grab, Unscrew banjo bolt and adapter. |
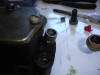 Place it in the other side. |
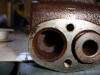 This piston is really stuck on this side. Typically brake side is worse than clutch side. |
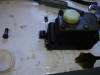 Start pumping the grease gun and watch it come out. |
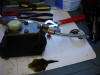 Once it is out enough, unscrew the banjo bolt and adapter. Use 101 of a grease gun is complete. |
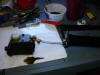 Easy as pie. Get ready for the mess. Fluid, grease and what ever was in there will be coming out. |
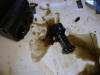 This one kind of shot out. Remember, be cautious when pumping pressure into this. Also Safety Glasses would be a good idea. |
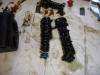 Now for the messy part. Grease everywhere. |
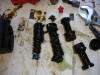 Now that you have springs, pistons and old rubber out. |
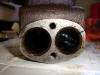 Wipe out bores and check the damage. |
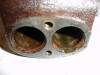 This particular one is in very good shape. There is only some surface rust and hardly any pitting at all. |
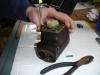 Now go to top and take off lid. |
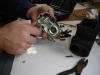 Use putty knife or screw driver carefully as typically lids are aluminum and can be easily damaged. |
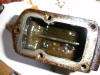 Empty reservoir of any remaining fluids and note condition of surface where lid fits. |
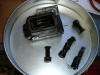 Place everything in pan. |
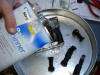 Pour a grease / dirt eating solvent. I use paint thinner which isn't good on rubber, but all rubber will be replaced. |
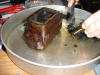 The grease will be pretty thick on everything, use detail brush or small wire brush to clean items. Soak core for 15 / 30 minutes to loosen grime. |
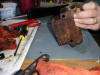 If rust is thick on exterior, take putty knife and scrape as much as you can. It will make sand blasting easier. |
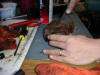 Spray core with carburetor cleaner all over, this will eat paint thinner and prep surface for sand blasting. |
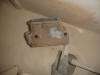 Make sure it is completely dry before sandblasting. Carb cleaner is perfect for that. Do a good job blasting as it will show at end. |
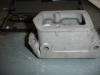 Get it all, this is longest process. |
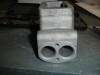 You are over the hump now. It is now rebuildable core. |
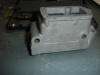 Inspect and make sure you got it all. |
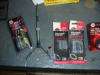 Get your hone ready with 220 medium grit hone stone. IF there is severe pitting, at this step it should be sleeved. |
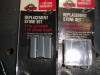 You can buy stone refills at auto part stores for approx. $3.50. these are the 1" stones. |
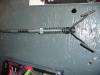 Hone for 7/8" bore. you can pick this up at most auto parts stores for approx. $15 -takes 1" stone cartridges. |
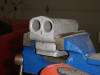 Set core in clamp and put your safety glasses on. |
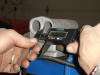 Measure your bore diameter and it should be .875 or close to it. |
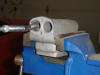 Put hone in high speed drill, insert hone before starting drill. Be cautious, parts may fly. |
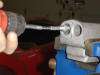 Slowly move hone in and out evenly first using the 220 medium grit stones. |
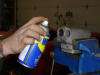 Make sure you keep the stones lubricated. |
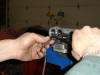 Continue to check the diameter. It will not change much using these grits of stones. Do both cylinders then use the 400 Grit stone same way. |
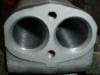 When honing is complete, you should have a nice smooth cylinder walls. Maximum safe diameter size is .885 which is about .010 larger than starting. |
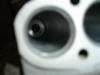 It is important to have honed it evenly throughout entire cylinder. |
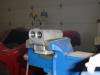 After cylinders are completed. Put wire brush in drill. |
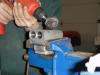 This process brings the core back to origional finish. It will look like it came right from the cast. USE SAFETY GLASSES. FLYING METAL HAIRS. |
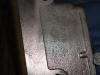 Shows difference, bottom brushed top still sand blated finish. |
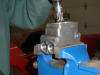 Use a very stiff wire brush to clean inside of reservoir. |
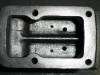 Very important to get reservoir clean and clear of any debris. If anyting gets into the cylinder from here, it could cause master cylinder to fail. |
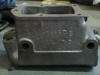 Exterior is finished. |
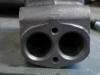 Bores finished. |
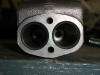 Double check cylinders after working on inside reservior. |
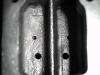 Reservoir finished. |
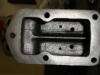 Looks beautiful. |
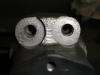 Make sure there is nothing stuck in these holes as it could make its way into cylinders and again could make master cylinder fail. |
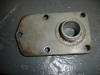 Now to work on lid. Check over it make sure no cracks. |
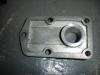 Make sure butting surface is clear of any debris where it meets with core. |
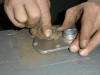 I use super fine grit steel wool to polish the aluminum lid. It brings a nice shine to it. |
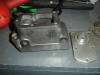 Core and lid complete. |
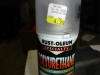 I like to take some polyurethane and spray the exterior. |
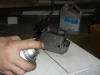 It puts a clear coat on it and keeps master cylinder from rusting. |
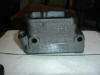 Hard to even tell it was sprayed. |
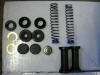 Ok, now the rebuild kit and guts. |
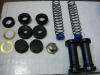 Check pistons for pitting, buggered edges, rust. make sure springs aren't cracked or expended. |
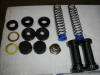 Rubber rebuild kits can be purchased for approx. $13 from Moss or other retailers. Pistons and springs can be also. Double check rubber for defects. |
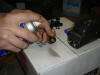 Lube the cylinder walls and rubber pieces. Do NOT use WD40. Use only brake fluid or red rubebr grease. |
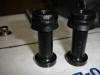 Put rubber seals on pistons. This can be a frustrating task as you have to get rubber over large end of piston. Lube it up. |
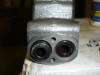 Hardware is different for each cylinder. Brake side has extra rubber ring and back flow valve. |
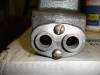 After you get guts in, put gasket on and front cap. Make sure pistons are in straight and not in a bind. |
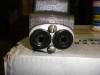 Place rubber boots on front plate. |
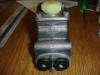 Place lid on and cap. I would recommend always replacing cap during restore. These plastic caps can be cracked and not know it. |
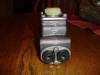 Critical: when putting lid on, make sure surfaces are flat and free of any debris. Don't over tighten screws. It doesn't take much to get good seal |
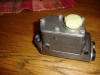 with cork gasket. |
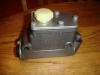 Your master cylinder is as good as new. |
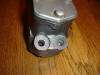 Check over everything, make sure you don't have any left over pieces. Throw all old rubber in trash as it should never be used again. |
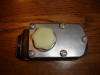 Double check to make sure new lid fits securely and has no cracks. |
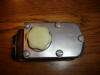 Double check all screws are tight. Hand tightened not torqued. |
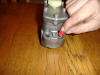 Last but not least, until it is ready to go back into your car, cap up the open holes. Thank you. Chad Pagel |
|