The MGA With An Attitude
CRANKSHAFT BEARING DIMENSIONS -- CS-106
At 05:32 PM 4/26/05 -0600, David Gills wrote:
"1961 Elva Courier - Would you happen to know the original ID & OD on a set of main bearings I have w/o measuring them? They are marked with a "P&V inscribed in a circle" and have the numbers/letters- 4341 12H62 ....."
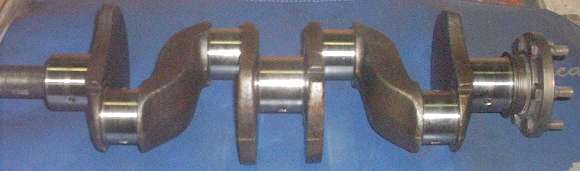
I will make the rash assumption that this is a 1600 engine (crankshaft interchangeable with the 1500), not the 1622 engine. I was just measuring the inside width across three spare main caps here, and I came up with 2.146. I was also measuring the big end bores on my spare set of rods, and come up with 2.021 (on the 3 good ones). That makes good sense, as there is .125 difference between main and rod journal diameter, and presumably the bearing shells might be the same thickness.
All of this got me cranked up to go try out my new dial bore gauge. I bought it for measuring cylinder bores, but it seems to work as well for bearing cradles. It has a dial gauge read out in 0.0005 inch increments. It is easily repeatable to even better accuracy, but is a little tricky to set up for the initial base dimension. It has a range of 2 to 6 inches, and the big ends are just over 2 inches without the bearing shells. I used a 2 inch micrometer for the initial setup to zero the bore gauge. Initial dial caliper measurement makes the big end bore close to 2.020 diameter, so I add a precision .0200 shim (included) to the bore gauge pin to put the dial on zero at 2.020 diameter. Then when measuring the big end bore it shows +.0010 on the dial, so the bore must be very close to 2.021.
For a cross reference check I put the old bearing shells back in the big end, but positioned them so they hang out one side of the cradle about 1/4 inch. Then I torqued up the bolts to make it secure and round out the bearing shells, and proceed to measure the OD of the bearing shells with a dial caliper and with a micrometer. This also comes out to be 2.021 inch, which makes me feel good about use of the dial bore gauge. Then I used both the bore gauge and a dial caliper to measure across the width of the spare main bearing caps (best as possible without being in assembly with the block). Here I get 2.146, which is exactly 0.125 larger than the big end bore.
Additionally I used a micrometer to measured the thickness of the un-worn end of a big end bearing shell (several of them). It's a little tricky measuring the slightly curved surfaces, but fairly accurate if only overlapping the micrometer a small amount onto the surfaces. Here I measure 0.072 inch for the thickness (radial thickness of the bearing shell).
For my bore measurements with the dial gauge I feel confident with all the numbers being accurate to within +/-0.0010". Additionally, the dial bore gauge is easily repeatable to within 0.0005 inch total range, so it is very easy to tell if the bore is out of round.
Now the stack up of dimensions looks like this.
Pay attention to min and max and how they add up.
The bearing largest bore will be found with smallest crankpin and largest clearance.
The bearing smallest bore will be found with largest crankpin and smallest clearance.
OD 1.8759 to 1.8764 Crank pin standard diameter spec.
add 0.0016 to 0.0001 Oil clearance (on the diameter)
total 1.8775 to 1.8765 Bearing bore spec (new and unworn)
For the con-rod big end cradle diameter,
Largest allowable diameter will be smallest shell bore plus largest shell thickness x2.
Smallest allowable diameter will be largest shell bore plus smallest shell thickness x2.
add 0.0715 or 0.0720 Bearing shell thickness (one side)
add 0.0715 or 0.0720 Bearing shell thickness (second side)
total 2.0205 to 2.0210 OD of bearing shell or ID of big end bore.
Notice this does not allow any tolerance error for machining the cradle bore in the big end of the con-rod. There must of course be some machining tolerance here, no matter how small it may be specified. There is therefore some rash assumption that not all tolerances will build to a worst case condition at the same time. To cover your tail in this case someone needs to check the final results after machining to assure that the oil clearance actually is in the specified range after machining and assembly.
One thing that bothers me some is the book specs for oil clearance in the 1500 rod journals. By the book it could be as little as 0.0001, which I think it impossible as it would not allow for any oil flow for cooling the bearings, and friction would make them promptly overheat and melt the white metal. The 1600 spec is .0010 to .0025 (.0009 larger), which is reasonable. I don't know why there would be a difference, because the 1500/1600 cranks are the same part number. Possibly the later dimensions supersede the earlier ones in production, so any replacement part would have the later dimensions. [As it turns out later, the second bearing has a different factory part number].
Since the spec's for the 1600 crankshaft are otherwise supposed to be the same as the 1500 parts, it would imply that the con-rod big end cradle bore would have to be about 0.0010 larger to provide the specified increased oil clearance. There is otherwise nothing in the book to explain how they arrive at different clearance for the con-rod bearings. If I split the difference and bump the big end cradle diameter up by half a thou it comes to total 2.0210 OD of bearing shell or ID of big end bore,
which by coincidence matches my actual measurement.
For the main bearings add 0.125 to all diameters, bringing the main bearing cradle bore up to 2.1460 diameter.
Change the journal OD slightly to account for any differences in oil clearance.
Reduce journal OD in 0.010 increments for regrinds.
Increase bearing shell thickness in 0.005 increments to match regrinds.
Dimensions found in the ACL bearing catalog for 1800 3-Main engine:
|
CONROD BEARING No. 12H33
Shaft: 1.8759/1.8764
Tunnel: 2.0210/2.0215
Max Wall: .0718
Clearance: .0009/.0030
|
MAIN BEARING No. 12H801
Shaft: 2.1265/2.1270
Tunnel: 2.2710/2.2715
Max Wall: .0715
Clearance: .0010/.0026
|
While the MGB part numbers (and main journal diameter) are different from MGA, the "Tunnel" diameters and wall thickness indicate that my dimensions for MGA are correct.
Click for a spread sheet detailing
Dimensions For The Mechanical Rear Seal and Main Bearing Cradles
|