The MGA With An Attitude
Master Cylinder PUSH RODS, MGA - HT-121
This is a brain teaser for the concours enthusiasts. See two different styles of master cylinder push rod in the picture.
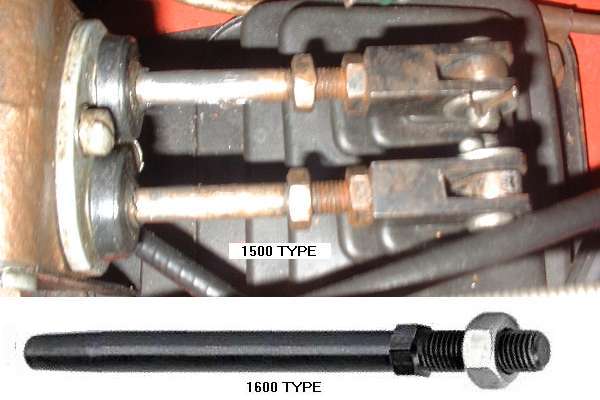
The push rod is 5/16 diameter with a slight taper at the blunt end, so the rounded tip is smaller where it fits into the master cylinder piston, and with 5/16-24-UNF thread on the input end.
According to the SPL, the 1500 model is a plain rod with two hex nuts, implying that one of the nuts has to be jammed against end of thread to be one with the rod, providing wrench flats to turn and hold the rod during adjustment, while the other nut is used as jam nut against the clevis. The picture is from my 1500 car, and indeed there are two thin hex nuts (jam nuts) on each rod. For the record, I don't recall ever buying thin nuts in my life, so these must have been on the car when I bought it in 1977.
According to the SPL, the 1600 model has a cold headed hex in the middle of the rod, and one hex nut to be used as jam nut against the clevis, as shown in the lower picture (but even this is not exactly right).
According to the SPL's, both models have the same part number (BCA4046) for the master cylinder push rod. This means the early part is superseded by the later part, and all replacement parts will be the later style. So if you want the early style part for concours show, you either find a good original part or make your own.
Furthermore, according to the SPL's, all of the hex nuts are part number LNZ205, which is a zinc plated Nylock nut. I have no idea why a Nylock nut was specified, but that's what the book says. Since I have thin hex nuts on my 1500, I might be persuaded to believe this is an error in the SPL. Part number for a zinc plated jam nut is FNZ205.
As to why the design changed, I can take a wild guess (from a little engineering experience). When the system operates the pedal swings on an arc, and the push rod is misaligned, moving slightly up and down at the input. If the push rod is large diameter, friction in the socket between push rod and piston will tend to cock the piston slightly, which could cause friction and wear between piston and bore. Making the output end of the rod smaller diameter would reduce the piston cocking tendency slightly.
When these parts are in large enough volume of production it is probably cheaper to forge the tapered end rather than machining it. This is likely done in the same forging setup as cold heading the small hex in middle of the rod and cutting it to length (from a long rod of feed material). The tapered end then also reduces amount of steel used to make the part. The thread would be cut (or more likely rolled) after forging.
Photo below is the master cylinder pushrod for the MGA Twin Cam with Dunlop four-wheel brakes. When assembled the flat washer is secured in the master cylinder with a retaining ring. Pushrod for the clutch master cylinder is similar design but with different part numbers. With no wrench flats on the pushrod, the threads must run free to turn the pushrod with your fingers, or hold it with pliers while adjusting the jam nut.
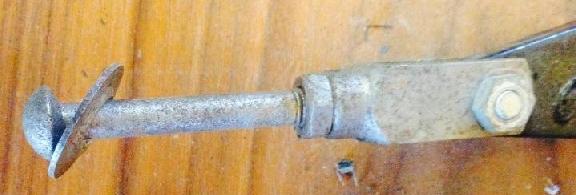
|