The MGA With An Attitude
VALVE CLEARANCE EYEBROWS - Page 3 of 4
Enter the steady helping hand that will hold the chosen implement of destruction. This is a hand held electric router that runs at 20,000 RPM or faster, similar to the speed of a hand held air powered die grinder. If you don't own one you can rent one for a day for a very reasonable fee. Here it is shown with the grinding wheel chucked up and ready to go.
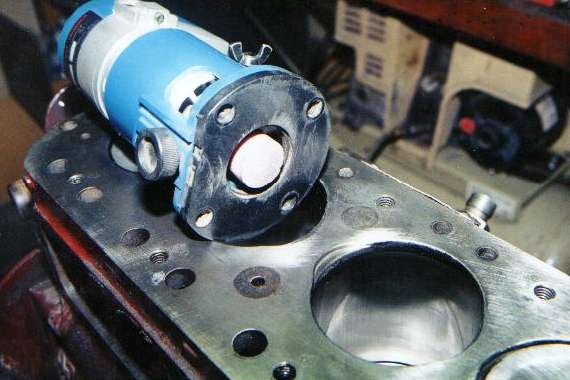
Below is a picture of the router with the grinding wheel adjusted to the desired .100" depth from the flat platen. This is one of those situations where you should measure twice and cut once, not wanting to accidentally butcher a good engine block. Also be sure that the height adjustment on the router is locked firmly in place so it can't move while you're intent on other things.
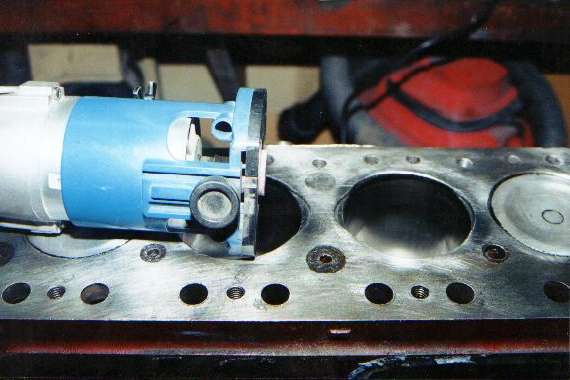
Now before you start grinding, if the pistons are still in the engine block you need to rotate the crankshaft to place all the pistons at about equal height around half way down the cylinder bores. Do not even think about moving the pistons while the grinding is going on. This grinding process produces copious amounts of fine iron powder that makes an excellent abrasive with the potential of tearing up the cylinder bores, pistons and rings in short order if you were to start moving the pistons with the grinding swarf still in the engine. I'm sorry I didn't get a picture of the small iron sand dunes in there, but trust me, it's not a pleasant sight. These pictures were taken long after the deed was done and the cleanup job was complete. Oh yes, and please remember to wear your safety glasses while grinding.
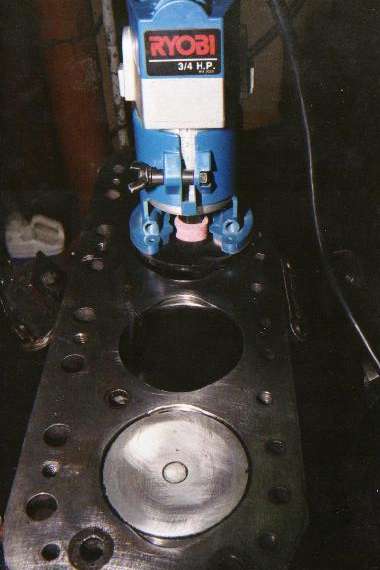
Okay, so while the grinding is going on the piston will not be at the top of the bore as shown here. During the grinding process I was holding a bright drop light in one hand and guiding the router with the other hand. With the grinding wheel turning at such a very high speed it can do a lot of cutting in a short time with very little force applied. Do not push too hard on the grinding wheel, as that would immediately remove the sharp corner from the wheel, and the resulting radius may encroach into the valve head clearance area of the eyebrow. Also check occasionally to be sure the height lock on the router is not slipping, which would result in deeper eyebrows than you had in mind (as well as slower going to remove more material). Be sure to keep the base of the router in flat contact with the top of the engine block at all times, nudge the tool gently into contact with the desired cutting point on the engine block from the inside of the cylinder bore, and never lift the router from the surface of the block. Keep moving the tool back and forth a bit to avoid generating a local hot spot. The cutting will seem to go rather slow at first, but don't rush the job, just let the abrasive wheel do all the work. The smaller relief cuts for the intake valves (1500 engine only) may only take a couple of minutes each to complete, the wider cuts for the exhaust valves may take more like 5 minutes each. With a little persistence the entire grinding job may be finished in about a half hour. With a little rotary rocking wrist action on the router you can easily create a nice arc in the metal. As it proceeds you can keep an eye out with the bright work light and sneak up on the scribe line you put down earlier. As the cutter will be proceeding quite slowly it is fairly easy to finish the cut very close to the prescribed arc markings. If you overshoot the ends of the arc a bit that's okay too, as it just takes off the small sharp corner at the junction with the cylinder wall and removes very little material there.
|