The MGA With An Attitude
WELDS And SCREWS in the TOP FRAME - TT-108C
On 8/15/2009, Dave Headrick wrote:
I found it curious that all three of the top bows were welded (small weld about 3/8" - 1/2" long) to the side linkage assemblies in addition to the screws which hold the parts together. Do you know if this factory original?
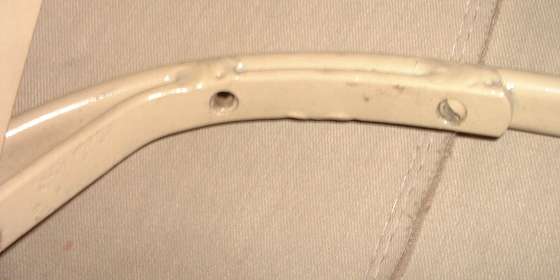
I have changed my tune on this a couple of times. I have seen them both ways, welded and not welded.
I am pretty sure they are original factory issue both ways. The welded ones all have the same welding pattern nice neat MIG welds, very consistent like they were all done by the same hand. As a career machine design engineer I would say that the screws alone will not (a least should not) hold it secure for long. There are no dowel pins or square corners for the parts to lock together, so there would be constant stress on the screws every time the frame is moved, raised or lowered, or subject to vibration. If you made the screws very tight and used thread lock adhesive they might stay put. Otherwise the screws would eventually work loose from relative motion between the parts.
My first impression was that the factory folks only figured that out after the parts were in production with screws only, then began welding the parts after assembly. This may have happened fairly early in production. If that was true there would be no need for the screws, just use some punched holes and alignment pins for fixturing prior to welding. Perhaps after the fact they figured it was just as easy to use the screws for fixturing prior to welding rather than changing the design to eliminate the screws and then having to build a welding fixture. You never know. Fifty-five years ago when labor was cheaper they might have figured it was cheaper to screw each one together rather than building a welding fixture.
On the other hand, I recently saw a 1962 1600-MK-II with the later style articulated frame, and that one was not welded. So did someone decide later on that the welding was wasted time as not necessary? Maybe it was a quality control thing, done at a time when the screws were not consistently tightened.
Addendum, November 15 2010:
This question has come up a few times: "What size and type are these screws"? Here again I have changed my tune a couple of times. One time I removed one from my top frame to check, and found it to be a slotted #8-32-UNF x 1/2 grommet head screw (domed countersunk head). I didn't record that fact anywhere, so more recently I wasn't so sure.
Today I removed a screw from the rear bow to check, and found it to be a #8 x 1/2 thread forming screw (commonly called self-tapping). Trusting prior memory, I also removed one from the first steel bow, and found it to be #8-32 fine threaded machine screw. See picture of these two screws. Both of these screws have 90-degree countersink angle, so they are both British standard, not Unified standard screws.
Being overtly curious, I proceeded to remove a few more screws for inspection. I find all screws in the rear two bows to be #8 tapping screws. Three screws in the front bow are #8-32 fine thread while the fourth screw was missing with stripped female thread. Now I suspect some DPO had substituted fine thread machine screws for replacements in some prior life (maybe it was me, 25 or 30 years ago during the first restoration).
To fill the open hole I ran a tap through it and installed a #10-32 x 1/2 grommet head screw (now cut to 1/2-inch long). That works as well, and there is hardly any discernible difference in the head size after installation. Trick is, this screw is one that is normally used to attach the dash mirror or flanged LTD studs for the tonneau cover. As such, I think the screw is #10-32-BSF, which has smaller head than a UNF screw, and 90-degree countersink. A #10-32-UNF screw would have 82-degree countersink and larger head.
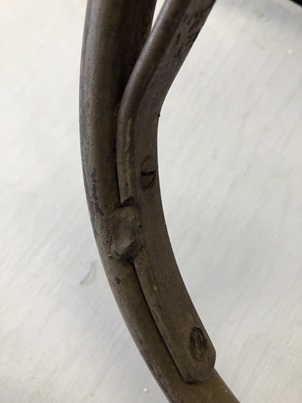
Here is a picture from a later production top frame where there are no welds on the front steel bow, and single welds on the middle and rear steel bows. The presumption is that the front bow is intended to be disassembled during installation of the canopy to allow a sewn in sleeve to be slipped over the front bow.
|