The MGA With An Attitude
MGA Windscreen TOP CORNER BRACKETS - WT-105
Below is the content of an instruction sheet included with a shipment of Moss Motors supplied top corner brackets for MGA windscreen.
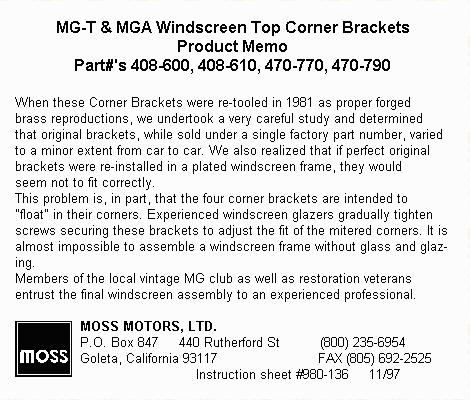
Here are a few pictures I first published after MGA Windscreen Tech Day in January 2002. You may refer to that photo report for more details of the fitting of these parts and complete windscreen assembly. I am posting this as a separate page because the discussion about fitting these parts keeps popping up repeatedly. I will not repeat the entire article here, but some details bear additional "clarification".
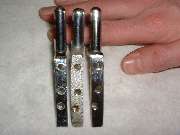
The part in the center is an original bracket as installed on the car from the factory. It is a 100% brass casting with chrome plating.
The part on the right came from Moss Motors in November 2001, and is the same part they have been supplying since 1981. It is a 100% brass casting with chrome plating as original, but unfortunately it did not fit MY windscreen. The angled part of the bracket was too thick to fit into the slots in the windscreen frames, even when NOT re-plated, and it required considerable grinding on both sides to thin it down enough to fit. This was not just interference caused by the thickness of plating, but substantially more. I had to reduce the thickness of the part by about .015 inch before it would fit into the mating slots. Some of the threaded holes were far enough out of position that the screws could not be installed without enlarging (or elongating) the holes in the frame. This is generally unacceptable for a couple of reasons, the first being obvious damage to the chrome plating on the frame. The two top screws are grommet head screws (slightly domed), and two of the side screws are flat head screws, all of which fit into countersunk holes in the frame. When these are misaligned the screw heads will not seat fully down into the holes and may remain standing proud of the surface. If you are having the frame re-plated, I STRONGLY suggest that you test fit these parts first, and do any modification to the frame BEFORE plating.
Most significantly, the top post on this Moss Motors supplied bracket is fixed at the wrong angle. Where it should be perpendicular to the top leg of the bracket it is actually parallel to the side leg. As such, when in final assembly the two posts are not parallel but are canted inward at the top. If the mating bushings in the convertible top front bow have sufficient clearance this might actually work, but this is by no means similar to the original parts, and the difference in appearance is very obvious. I have brought this point to the attention of Moss Motors, first in 1986 and again in 2002. This Moss part remains the same as of late 2005.
The part on the left came from Clarke Spares and Restorations, designed by and special made for Todd Clarke. The angle part of this bracket is made from rectangular steel strip stock, bent and drilled and tapped. The top post is a brass screw machine part with a reduced diameter pin at the bottom which is staked (riveted) into the steel bracket, and the part is then chrome plated. This is a very strong bracket and a perfect fit (in MY windscreen). In assembly the visible post is indistinguishable from the original part.
Reference CSM MG/232, September 1958:
Windscreen hood pegs changed from plated brass to plated mild steel to increase strength. Commencing car no. 57100. Parts interchangeable.
The last picture on the far right above shows a pair of 1/8 inch thick steel spacers that I made to help with the preassembly (without the glass). The top corner brackets fit with a small gap between the side leg and the inside of the frame of the windscreen. I presume this is intentional, so that in final assembly the screws will pull the frame pieces tightly together at the mitered corner joint without leaving a gap. It all works quite well without these spacers at final assembly (as long as the screw holes are in the right location). But it was convenient to have these spacers installed while trial fitting without the glass there to hold the parts in correct alignment. This is the only joint in the entire assembly which finishes with an air space between the parts connected with the screws.
The bottom corner brackets might be allowed to "float" for alignment during the process of assembly, but will be tight against the frame when finished.
Addendum May 2011: The Moss Motors catalog now shows two different part numbers for each of the two top corner brackets. The first numbers 470-770 and 470-780 are unchanged. I have not seen new parts since 2005, but (rashly might) assume that the parts are also unchanged. The new numbers 470-775 and 470-785 are "undrilled". That being the case, the LH ad RH parts might be the same (before customer drill and tap). I have not seen these parts yet, so do not know if material has changed or if the peg angle has been corrected. End user comment would be welcome.
|