The MGA With An Attitude
Clarke Spares & Restorations, Chalfont, PA - (October 20-21, 2023)
Friday, October 20, 2023:
We had an appointment to meet Tom Zofchak of British Miles (Morrisville PA), at the prior shop of Clarke Spares and Restorations (Todd Clarke, deceased), in Chalfont, PA. British Miles has purchased the business and everything within, exclusive of the building space which was (and still is) leased. We may help some with moving, but are really here to see what we can do to promote the moving and restocking in the new location, and getting this merchandise back on the market, available to the customers. There is also manufacturing machinery and tooling for making lots of unique parts that no one else offers. Lots of people have been asking, "What happened to Todd's stuff? When is it going to be available again? Is British Miles going to resume and continue production of Todd's special parts? When, when, when? We're anxious".
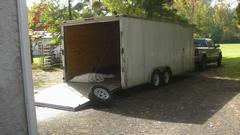
We were delayed a bit in front of the paint store, blocked by a fork truck unloading a semi, but a few minutes later it cleared out so we could get behind the building to the rear doors where Todd was doing business. Step inside and start taking pictures, for all posterity, and to make note of everything that is here, for the purpose of planning how to move everything, and what to do with it after moving. Sorry for the small manual fork truck and roller tables in the way, but I don't have an extra wide angle lens, so some of these pictures will be somewhat restricted and/or cluttered. To the right of the entrance doors, a view of the loft with who knows what (or why), The room below that loft has tables in the middle of the room and shelving around the sides, obviously space for shipping and receiving. The "BIG" machine is a bending brake for forming long strips of metal into "V" or "U" shapes, like MGA under dash braces for instance.
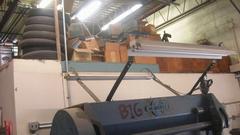
Looking along the right side of the room, the "BIG BLUE" machine is an even larger press brake for forming heavier metal, like MGA floor support rails for instance. To the left of the old heating stove, behind the belt sander, the machine with the orange flywheel is a small size punch press. There will be several of those here in a wide range of sizes. A step to the left, the green machine with the larger flywheel is a much larger punch press, weighing a few tons, capable of punching out and forming heavy gauge steel parts. A few steps farther left, another green machine is a mid size punch press. Reason for so many presses is not just material capability, but also to have multiple tooling set-ups and not have to swap out the press dies so often. Notice between the two green presses, stacks of large rolls of steel strip stock, raw material feed stock for the presses.
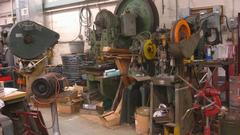
Back a few steps, and looking left, the thing that looks like a fat electric motor is (I think) a burnishing machine used for polishing metal strip stock (maybe). The wide green machine is the back of a PEXTO sheet metal shear. The smaller red machine(s) on the floor may be strip straightening machines for undoing rolls of metal and straightening it out to se straight flat strips. Behind against the wall, a small tractor tire, as Todd was also into making parts for Gravely garden tractors. A heavy duty Singer sewing machine, good for stitching up durable fabrics like leather and heavy vinyl, or multiple layers of heavy cloth or construction board, think seat covers, convertible tops, tonneau covers, interior kick panels, and covering cockpit trim rolls. The green thing beside that is a multi-purpose arbor press.
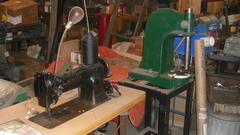
Walking around the end to comeback we have the front working side of the PEXTO shear. A fairly large general purpose lathe. Then a mid size drill press.
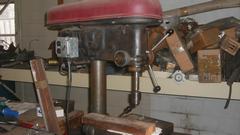
A surface grinder, maybe not do much for making car parts, but useful for making machine parts for the punch press dies. The gray thing is a hand operated cam actuated punch press. The green machine with the long handles is a hand operates bending brake, about 18-inch width capacity, hefty enough to handle fairly thick sheet metal.
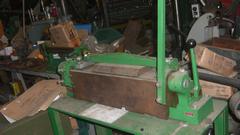
The gray device is a manual wrap forming machine, and the "P" shape piece hanging on it is an example of what it can do. The black roller type fellow is a bead rolling machine, and shape of the mating silver rollers on the end is an example of the shapes it can roll into strip metal stock. The two fixtures below it are manually operated metal wrapping machines, primarily used for forming round wire parts. The hand operated roller machine is good for flattening and thinning sheet metal. If there is a third roller hiding behind, then it could also curl sheet metal into cylindrical shapes.
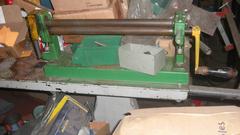
The big gray guy is a drill press, currently sporting a fancy step drill or reamer. There are more capabilities, like if you want to put a tapping head in it for quickly making a lot of threaded holes. Another rolling machine. With the right mating ridge and groove rollers,it can form flanges or multiple ribs in sheet metal. Then a heavy manually operated punch press, and a smaller manually operated bending brake.
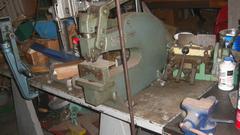
Getting sketchier as we go, some of these little machines have me scratching my head. The hand cranker is an Easy Edger, used to roll a "V" line in sheet metal,like forming a flange on the edge of a piece, any angle up to 90 degrees (or maybe more), and it could be a curved edge. The pedestal tools have interchangeable tool heads for multiple purposes. Then another drill press, and this one definitely has a reversible tapping head with the car part it is tapping into right below the tap. The big green beast is a turret lathe with multiple cutting tools in the turret for doing multiple turning cuts on a single part.
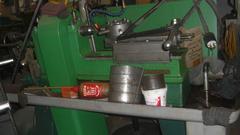
There is an engine generator (on wheels) that can do 240VAC output. More punch presses. The green one on left looks like set up to to make some custom size flat washers, or maybe flanged holes in sheet metal. The larger press currently without tooling. The red device on the right is se up for feeding strip steel to feed the press(es). Hiding in between a bit farther back is a welded sled runner assembly for children's sled. Todd was making some sheet metal parts for those as well. Another punch press with some odd tooling that I don't recognize. Have we lost count of the presses yet?
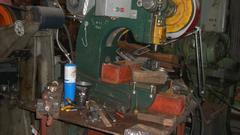
Two more close up views of the largest presses in the shop, along the right wall, which were shown near top row of these pictures. A larger belt sander, and another stack of coiled steel strip stock.
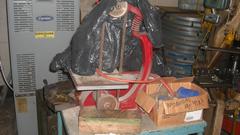
An industrial capacity sand blaster, and the large air compressor to power it. Not to fear, it is not radioactive. The wide belt sander, considering color and amount of dust, may be used to finish edges of poly panels for side curtains.
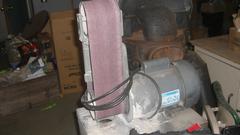
There would be a couple thousand square feet of high rise pallet racks and shelving holding I think thousands of different part numbers of finished parts, as well as a lot of raw material used in production. Finished parts are commonly fairly small metal bits, but can be dense and heavy in large lots. The third picture below with low shelves was an in-out materials handling ares. Todd was big on packaging fastener kits for things like interior panel screw sets and body wing assembly bolts. This could involve up to 20 boxes of different fasteners on the input side, moving into a large stack of identical packaged assortment fastener kits on the output side.
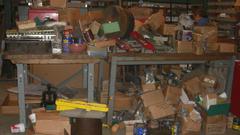
All of this stuff has to be bagged or boxed up for moving. Each package not too big, but lots of this stuff can overload trucks and trailers. Eventually the heavy pallet racks will break down to be moved as well.
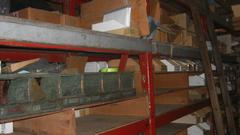
Remember this row of pictures, as there will be another review later.
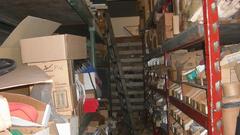
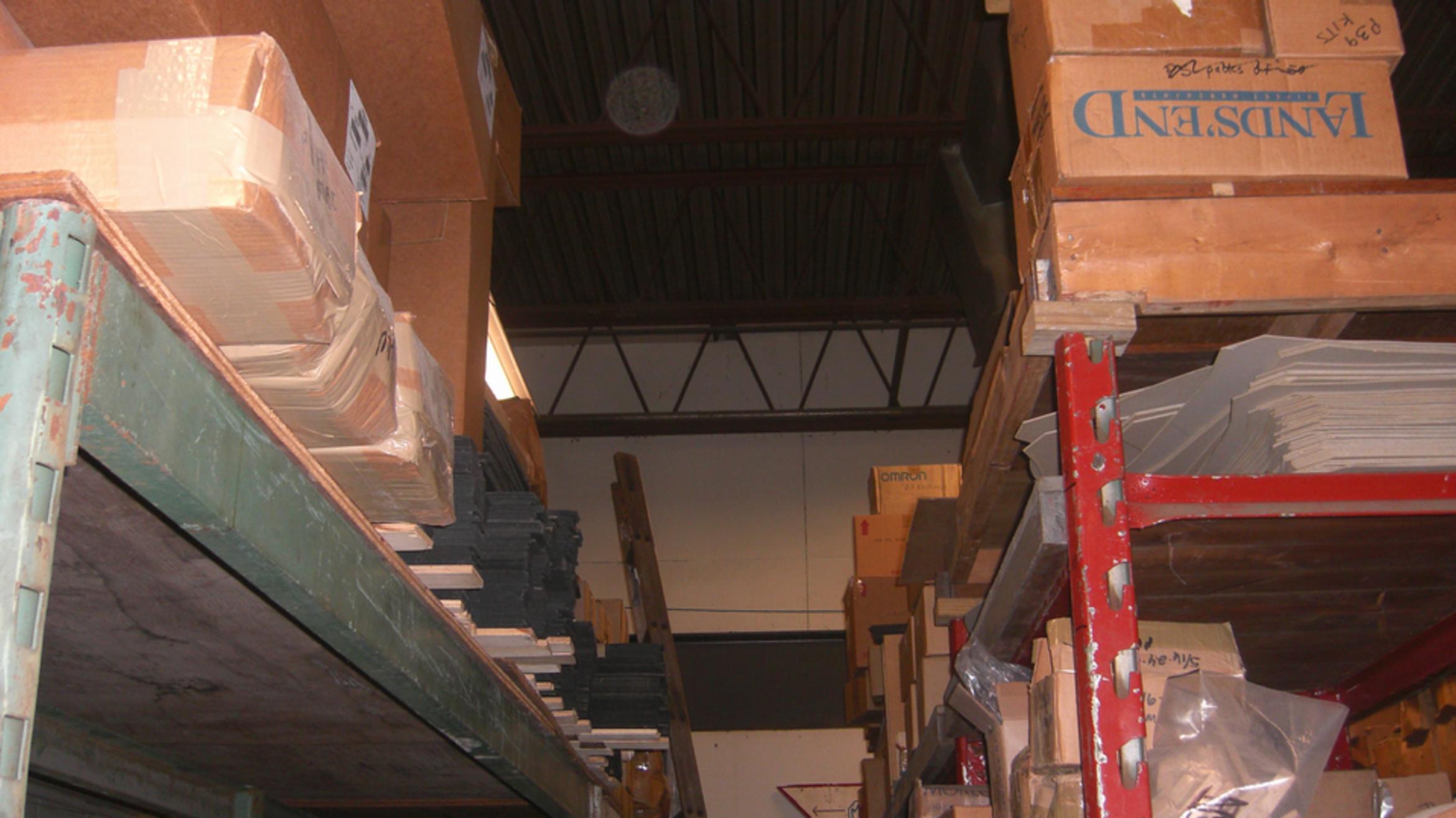
A lot of what I was doing today was identifying unmarked parts and putting part numbers on them.
The package that looks like a bag of pennies was punch-out scrap from one of the punch press operations. Several pounds of clean brass is definitely worth recycling. One last look at a large punch press. I'm sure the MGA rear wheel bearing hub is just a coincidence, nothing to do with this press.
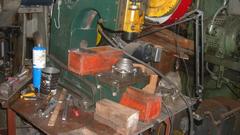
More stacks of strip steel stock. By now we can measure this in tons. Things behind the building are active machines. The large round gray thing is vibratory abrasive polishing machine. Material on pallets to the left is abrasive media. The cement mixer to the right is also loaded with abrasive, to be used for tumbling and deburring a lot of the stamped metal parts.
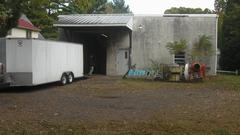
To answer a few ongoing questions, Todd passed away in January, and Tom bought the business with all of the materials and tooling shortly thereafter. It is now in the process of moving to the British Miles facilities, likely to take a few more weeks for the carry-out stuff, and maybe longer to move the heavy machinery. Existing materials and car parts need to be logged into inventory before the parts will be available for sale again. There is intention to resume and continue production of the car parts, but it will take a long time to get it all organized with the machinery re-installed and set-up for production.
Saturday, October 21, 2023:
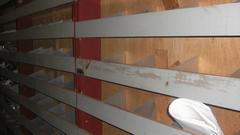
Back to the Clarke Spares shop, we spent a few more hours hauling heavy carts of inventory parts out to the trailer, until my old back gave out and screamed "no more". Some progress is showing, as the back wall of fixed bins parts has been all bagged and removed.
Sunday, October 22, 2023:
Finally finishing up the photos and notes from Friday and Saturday. We have appointments and some traveling to do, but we may be back next weekend.
|