Just a Simple Wrench
by Ann & Jake Snyder
Exactly the Right Length
We were touring in grand style, with the GT moving quickly enough to be neither the slowest nor the fastest car on the three lanes going south. Then there was a chirp from under the dash, and both of us grabbed for the shift lever and hauled back on it, holding it secure in top gear. It was not relaxing driving this way, because we constantly anticipated the jarring of the “overdrive on” alarm, a simple device that shrills loudly when the overdrive is switched “in” with the column switch but the gearbox is not in top gear. The point of the alarm is to protect the cone clutch (more formally, “sliding member”, see Bentley) from unnecessary wear caused by unknowingly accelerating with the overdrive engaged.
Our problem was that the gearbox would not stay in fourth gear. When we had first rebuilt it, every thing was fine, although we did have to replace the overdrive switch a lot sooner than seemed reasonable. But a fourth gear problem developed and definitely was getting worse. The gearbox felt sloppy when shifted into third or fourth and would slip out of fourth far enough to disengage the overdrive switch that is activated by the shift lever. When overdrive disengages, the engine must speed up, and the abrupt shock of the change in load on the engine is very dramatic. Doing this occasionally is hard enough on the gearbox (and U-joints, and clutch, and rear axle, and so forth). Having the car drop out of overdrive once a mile makes using the overdrive as frustrating as having one and not being able to use it. Besides, running without overdrive still caused the shift lever to move forward out of top gear occasionally when the car was not accelerating.
We first tried securing the gearbox and engine a bit more snugly to limit the front to rear movement. We reasoned that if the gearbox (and engine) moved forward a bit when decelerating, perhaps the shift lever boot was dragging enough to pull the gear lever. We tightened the stay rod nuts on the bar that runs between the front of the gearbox and the crossmember. This stay rod, which is not the fitted to all MGB models, limits the forward travel of the gearbox (and engine). Tightening this did not help the problem at all.
Next we tried repositioning the shift boot and gaiter. We did this on a long trip using the Phillips end of a 20-function fix-your-car-multi-tool. We never found a location for the shift boot and gaiter that was much different or that helped the problem. We even bought a really ratty gaiter that was permanently kinked to the top gear position. This did not help either.
Then we talked to fellow clubmembers. One response was, “Mine pops out of fourth gear, too”. No consolation there, just commiseration. Another club member suggested that the “slider”, the part that the shifting fork moves from third to fourth gear, could be badly worn. Checking the price on this part made us think of the fortune we missed when we did not load up on twenty-five dollar gearboxes at the swap meet. We looked in the books. All they said was that the detent springs in the synchromesh hubs could be broken. In any case, changing either the synchromesh hub detent springs or the slider would mean removing the engine and gearbox again, and we were still getting over last year’s adventures in that area. What we needed was a quick fix that would not result in excessive wear on the gearbox internals.
We rejected without thought or comment the bungy cord approach. Being able to shift is part of the joy of an MG, and disconnecting a bungy cord first is not acceptable from either a functional or esthetic viewpoint. Looking hard at the exploded diagram (this is a four-synchro later model gearbox) showed one possibility where the detent plungers on the shifting rods could probably be loaded with heavier or more springs to help hold the rod in the proper gear. And these, possibly, were accessible without removing the gearbox from the car.
There is one detent plunger for each of the three shift rods. Each detent plunger is held down with a spring, and each spring is kept in the case with a bolt that is most likely a fine thread three-eights inch. The position of the bolts (and hence, the shift rods) are as follows: farthest left is the reverse, the center is for first/second gears and the innermost operates the third/fourth shifting fork.
It was the innermost to which we needed access. It is possible to remove this from under the car (be very careful with jacks and jackstands) by hugging the gearbox with both arms and simultaneously using a short nine-sixteenths socket. After removing the bolt, the spring and plunger were easily removed with a magnetic probe. Naturally, the magnetic tool must fit easily in the hole, and must be checked for an adequately small diameter by passing through a fine thread three-eighths inch nut. If the magnetic pickup tool sticks in the hole, the plunger will never come out. Then we were ready to hunt up some really strong springs to help us live with our sick gearbox.
But inspection of the plunger showed it was a big part of the problem. The bottom of this plunger should have been round to fit into a corresponding depression in the shifting rod. Instead, the bottom was worn flat. We knew it had been round when we assembled it, and it had clearly worn away in twenty thousand miles. As we are fortunate in having a few extra gearboxes about, we retrieved a used plunger, noting that it was almost a quarter inch longer than the one we had taken out, allowing for the exceptional wear where the round tip had been. Just to be sure, we checked a second gearbox, and it also had a long plunger in the third/fourth position. We installed one of the longer, used plungers, and, with the proper length plunger in place, the gearbox worked perfectly again. It even felt good again. Apparently, we had put the wrong detent plunger in the third-fourth shifting rod hole. It was just long enough to wear in the detent when it should have held solidly, and the constant slipping caused the plunger to be worn flat.
We checked our parts manuals and catalogs, but never did get a clear idea of what the part numbers or the descriptions of the various plungers really were. In fact, there was not even an indication that there was more than one length of plunger. We know we will have to rebuild other gearboxes, and we wanted to be certain we get the plungers back in the right holes, and the question of where the short plunger should have gone was important to us.
We are really fortunate in having had possession of one gearbox for about thirty years, and we are certain it has never before been dismantled. In fact, it has spent several restful decades in the boot of one of our garden ornaments. We recovered this priceless artifact to chronicle the secrets of its shifting rod detent plungers and springs. The springs were all about the same length, measuring between 0.850 and 0.900 inch. The surprise was that all the detent plungers were 1.440 inch. Estimating the round portion of the defective plunger, we think the short plunger was about 1.23 inch before it wore off in the detent on the shifting rod.
The question of from where the short plunger came is worth considering. Obviously, it had been in the gearbox when we disassembled it the first time, and it could not have been in the third/fourth spot or it would have already been worn out. The same argument holds for the first-second position. The most likely place would have been the reverse plunger. Do you suppose it is possible that the factory did not have enough of the proper 1.440-inch plungers, and used either plungers from a different model gearbox or used a shipment of defective parts from a supplier? And that the workers knew that the short plunger would not wear out noticeably in the reverse detent because reverse is usually used for only a few car lengths? If either of these suggestions is true, then there are more than our gearbox with this potential problem. Could one of them be yours?
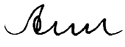
|