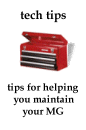

Chicagoland MG Club
General Tips
MGA Tips
MGB Tips
Midget Tips
MGT Tips
MMM Tips
Tech Session Photo Archives
|
|

Shock Absorbers
Shock absorbers, especially the lever types found on many older British cars, are a bit of a mystery to many people. Exactly what they do and how they do it are often misunderstood, as are the effects of using "stiffer" than stock shock absorbers.
A car without shock absorbers bounces and wallows after hitting a bump or a pothole, and rocks from side to side when entering and exiting turns. Bumps on corners tend to produce wild uncontrollability. These effects are worse on heavier, softly sprung vehicles. Shock absorbers control these actions by damping the spring oscillations, and slowing motion of the body on the suspension. Shock absorbers do not affect the spring rate (stiffness), nor the amount of body roll or pitch; they control how fast movement between the body and suspension takes place. A given weight will produce the same change in ride height with or without shock absorbers. The same weight dropped from a two foot height into the trunk of a car with bad shocks (or none at all), will cause the car to bounce up and down four or five times. The same weight dropped from the same height into the same car with good shocks will cause the rear of the car to go down, rise a little, and be still.
Hydraulic shock absorbers operate by pushing oil through small holes; the smaller the hole, the more resistance. Unfortunately, such a plain orifice is unsuitable for practical applications, as the resistance increases as the square of the oil's velocity. A simple orifice of a size producing the desired action on a normal road at low speed would produce an essentially immobile suspension at high speed on a rough road. This is overcome by the use of properly calibrated orifices and spring-loaded valves, as well as careful selection of the oil used.
Shock absorbers are designed for a specific set of conditions: vehicle sprung weight, unsprung weight, spring rate, suspension travel, tires used, and driving conditions, among others. "Stock" shock absorbers are a good compromise to suit a particular vehicle for its intended use. The front shocks originally fitted on the TR2, for example, were found to be slightly too stiff for normal touring, allowing front end "patter" between 60 and 70 mph. The change to slightly "softer" shocks in 1956 solved the problem. A shock absorber with the same settings as the discontinued one was added as a competition item, although it was of slightly increased size for greater load capacity.
The basic principles of operation are the same for tube and lever shocks. The tube shock illustrated clearly demonstrates these principles.
On the bump (compression) stroke, the oil pressure opens the piston valve, and oil passes through the ports in the piston from the lower to the upper portion of the cylinder. The excess oil displaced by the piston rod passes through the ports in the piston rod guide, down the anti-foam tube and into the reservoir (the space between the inner and outer tubes) by way of the rebound valve . On the rebound stroke, the piston valve closes and oil passes through the ports in the piston rod guide, down the anti-foam tube, opens the rebound valve and passes into the reservoir. At the same time, the foot valve opens and oil is recuperated into the lower part of the cylinder. General slow speed damping is, however, accomplished by bleed orifices in the valve mechanisms. Full valve action is designed to occur only during more severe action. This is true of lever shocks as well.
It is easily seen from the illustration of the lever shock that when the arm is moved upwards ("bump" or "compression" stroke), the compression piston "E" moves downwards, forcing oil through the ports, and building up pressure until the compression valve "F" opens against its spring. Oil within the valve chamber is forced into the opposite cylinder as piston "H" rises. On the rebound stroke, the rebound piston "H" moves downwards, forcing oil into the valve chamber, through the ports in the compression valve plunger, building up pressure until the rebound valve "G" opens. Due to lags in the flow of oil during pressure build-up and slight unavoidable leakage past the pistons, there is not a perfectly even transfer of oil between the cylinders. To account for this, spring-loaded valves are built into the faces of the pistons, allowing oil recuperation on upward piston movement. Since the Armstrong lever shock combined valve units are replaceable, valves of different specifications may be substituted to suit particular requirements.
While almost no tube shocks can be rebuilt, lever shocks can be. But do not try it yourself-you can't obtain new parts, and you have no idea what the tolerances and specifications should be. It is, however, instructive to disassemble a really "trashed" unit which is unfit as an exchange core.
The fluid level of Armstrong lever shocks should be checked periodically, and any fluid lost should be replaced.
Carefully clean around the filler plug before unscrewing it. The oil level should be at the base of the filler plug boss.
Back to General Tech Tips
|
|