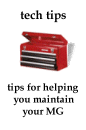

Chicagoland MG Club
General Tips
MGA Tips
MGB Tips
Midget Tips
MGT Tips
MMM Tips
Tech Session Photo Archives
|
|

Turn Signals:
Understanding Them and Making Them Work
If you have ever wondered how that simple-looking little three-prong flasher unit actually performs the task of blinking the turn signal lamps on and off this no-nonsense explanation should unveil the mystery. Beyond that, it will provide information of a practical nature which should be useful in diagnosing and repairing a faulty turn signal circuit. A 1963 TR4 was the vehicle which launched this project, but the information herein will readily transfer to other vehicles.

A real flasher unit was carefully dissected to make it reveal its secrets. It did so, reluctantly. The resistance heater, for example (see [9], Fig. 1), is a wire finer than a human hair. It is so brittle that it will usually break if an attempt is made to bend it sharply. It cannot be soldered. It must be spot-welded to the bi-metal strip (10). Since it is the weakest link in the electrical chain, it is the common source of trouble in the flasher unit. Even the adventurous do-it-yourselfer will find it much more economical to replace the flasher than to attempt a repair when it dies.
Fig. 1 gives a general picture of the wiring. It does omit a host of intermediate connections between the hot battery terminal and terminal #3 of the flasher. This is of no consequence in explaining how the flasher operates. (Do not despair. The omitted intermediate connections will be picked up in Fig. 2.) Note that all of the following components are on the plug-in flasher unit proper: (1), (2), (3), (9), (10), (11), (12) and (13) of Fig. 1. The small isometric sketch shows the terminal identification of the plug-in flasher in Fig. 1.
Theory of Operation
Assume the driver signals for a left turn by moving the turn signal switch (8) to the left turn position. An interesting series of events is then executed. These will be examined one step at a time while referring to Fig. 1.
Step 1. The left front and rear turn indicator lamps (4) and (5) are "cold"; their filaments have very low electrical resistance. Electrons immediately rush from the hot battery terminal to terminal #3 of the flasher, through the resistance heater (9), out of terminal #1 of the flasher, through the turn signal switch (8), and the cold filaments of the left turn indicator lamps (4) and (5).
Step 2. The turn indicator lamps (4) and (5) do not immediately come on, but their filaments do begin to heat up, and during this time period, current is flowing in the resistance heater (9).
Step 3. The current in the resistance heater (9) produces heat which is transferred to the bi-metal strip (10) since the resistance heater (9) is physically mounted on the bi-metal strip (10). The heat causes the bi-metal strip (10) to flex or bend by an amount sufficient to close the contacts at (11).
Step 4. Because the contacts at (11) are now closed the resistance heater (9) is electrically bypassed. Electrons from the hot battery terminal flow through the heavy wire windings of the electromagnet (12), out through contacts (11), to terminal #1, through switch (8), and through turn indicator lamps (4) and (5), turning them on.
Step 5. At this point three things happen simultaneously.
A. The current in the heavy wire windings cause the armature of the electromagnet (12) to be pulled to the pole of the magnet, closing contacts (13) which allow the green monitor lamp (15) on the dashboard to come on.
B. The extremely low resistance of the heavy wire windings (12) are bypassing electrons around the resistance heater (9), allowing the resistance heater (9) to cool down.
C. The heavy wire windings (12) are furnishing an electron path from the hot battery terminal to the turn indicator lamps (4) and (5) which therefore remain on.
Step 6. The turn indicator lamps (4) and (5) remain on until the resistance heater (9) on the bi-metal strip (10) cools sufficiently to allow the bi-metal strip (10) to return to its original position. This takes less than one second.
Step 7. When the bi-metal strip (10) returns to its original position the contacts at (11) "open" and two things happen:
A. Electrons can no longer flow through the heavy wire windings (12) on the electromagnet so the contacts at (13) "open", causing the green monitor lamp (15) on the dashboard to go off.
B. The electrons from the hot terminal of the battery can get to the turn indicator lamps only through the resistance heater (9) which, due to its high resistance at this moment, will not permit sufficient current into the lamps (4) and (5) to make them stay on. Lamps (4) and (5) go off.
Step 8. Since lamps (4) and (5) are OFF their filaments cool down, giving them low resistance. This lets heavy current flow in the resistance heater (9) and the whole sequence is repeated from STEP 1. This cycle goes on and on until the turn signal switch (8) is returned to the center off position.
Subjected to the scrutiny of careful observation the system is found to be simple in concept and clever in design.
Trouble-Shooting the System
Time will take its toll in corrosion and rust in all older vehicles. These culprits not only destroy body panels and structural members, they disrupt electrical systems in the most insidious manner. If the turn signals are not operating properly, the circuit may be diagnosed as follows. We are assuming the battery is at full charge, the ignition switch is on, and the flasher unit is good. Refer to Fig. 2.
1. Refer to the vehicle wiring diagram to determine if there is a fuse in the turn signal circuit. If there is, either replace it with a good fuse or confirm that the original fuse is good. Be absolutely certain that the fuse terminals and the fuse socket terminals are clean.
2. Inspect the lamps in the turn signal system and insure they are all good. A bad lamp may cause erratic operation of the flasher unit, since the operation of the unit depends on the cold and hot resistance of the turn indicator lamps.
3. Test the turn signal switch itself.
A. Remove the flasher unit from the socket.
B. Place a jumper wire from terminal #1 to terminal #3 on the socket itself.
C. Turn the ignition switch on.
D. Move the turn signal switch in position to signal for a right turn. The right hand front and rear turn indicator lamps should come on. They will not flash, but if they come on and stay on, the switch has passed the right turn test.
E. Move the turn signal switch in position to signal for a left turn. The left hand front and rear turn indicator lamps should come on. They will not flash, but if they come on and stay on, the switch has passed the left test.
Obviously, if the turn signal switch does not pass both tests, look for a malfunction in the switch, its contacts, and/or the wiring associated with the switch.
4. Remove the jumper wire from the socket and plug the flasher unit back into the socket.
Assuming the battery is at charge, the fuse is good, the lamps are good, the flasher unit is good, the ignition switch is ON and the turn signal switch is good, the turn signal circuit should be operating properly.
Ah! But suppose it does not! Now what?
The next logical place to look for trouble is in the lamp sockets. In most cases the "ground return" for a lamp is made by the lamp body simply touching the "ground" side of the lamp socket. You can imagine that over the years a great deal of dust, dirt and corrosion can build up inside the lamp sockets. If the sockets are simply dirty they may be cleaned with a bit of TV tuner cleaner, a toothbrush and some elbow grease. There are times when it may be necessary to resort to using household cleanser and a small wire brush chucked in an electric drill to clean the sockets. From the standpoint of safety it would be wise to use a battery-operated cordless drill. There is no sense in risking electrocution for the sake of repairing a turn signal system!
On some older cars, especially if the lamp sockets are made of aluminum, the sockets are often corroded so badly that no amount of physical scrubbing will repair them. The obvious solution is to replace the sockets if you can find replacements. Let's suppose you can't. (We're not licked yet!)
Some may look on this last resort as "cheating" and perhaps they are correct, but it will safely put the vehicle back on the road until replacement sockets are found. The last resort solution is this: Purchase replacement lamps with brass bases. Solder a pig-tail ground wire to the brass base of each lamp, thread the wire through the socket (even if you have to drill a hole for it) when inserting the lamp into the socket. Connect the pigtail ground wire to any good, clean ground, either in a nearby section of wiring harness or directly to a chassis bolt. The length of the pigtail ground wire will be determined by the distance from the lamp socket to the selected ground point.
If this last resort fails to restore the turn signal system to full operation it will be necessary to make a physical and eyeball inspection of the turn signal circuit, wire by wire. This is not as difficult as it sounds if an electrical map is drawn of only the turn signal circuit by consulting the vehicle wiring diagram. As an example, such a map is shown in Fig. 2. It is for a 1963 Triumph TR4. When making the map, indicate the wire colors to make the circuit tracing job easy when actually working on the circuit in the vehicle.
With the map in hand, begin at the solenoid (2) of Fig. 2 and follow wire by wire through the circuit. For instance, in Fig. 2, the lead from the solenoid (2) to the ammeter (3) is marked N. The color code chart shows that N indicates a brown wire. Make a visual inspection of the brown wire, paying special attention to the condition of the terminals at its ends. If they are dirty, corroded, or hanging by a thread of copper wire they must be thoroughly cleaned and/or replaced. If the decision is made to replace them be sure to solder the replacements to the harness. Do not trust a crimped connection to perform with the same efficiency as a soldered connection!
There are about 14 wire terminals in the circuit of Fig. 2 between the solenoid (2) and terminal #3 of the flasher unit (9). If each of these terminal-to-wire connections is just slightly inefficient it is easy to understand that the 14 poor connections in series add up to trouble in the circuit.
If a physical inspection of the individual wires seems to indicate that all is well, yet the circuit is not operating properly, we may temporarily bypass whole sections of the circuit with a jumper wire to make a test. Suppose in Fig. 2 we think there are some poor, hidden connections between the solenoid (2) and the flasher (9). A temporary jumper wire may be connected (see dashed line in Fig. 2) from the solenoid (2) to terminal #3 of the flasher (9). This temporary jumper bypasses the ammeter (3), the voltage regulator (4), the ignition switch (5), the fuse (6), the in-line connector (8) and all associated terminal-to-wire connections in the bypassed section. If the circuit now operates normally, or with marked improvement, chances are that the problem is in some part of the circuit that is being bypassed. For those vehicles over 15 years of age, oxidation at the terminal-to-wire connections should be suspected.
Inspect very carefully at points where the wiring harness passes through rubber grommets. Over the years, the rubber deteriorates, and road vibration can cause the wire insulation to wear through. Where this happens, the bare wire rubs on the chassis ground and can cause intermittent electrical problems if you're lucky. (If you're not lucky, the wiring harness simply catches on fire, resulting in considerable unsolicited attention from bystanders.)
And now a word about oxidation. Oxides are the compounds formed when metals combine with oxygen. Oxides are insulators. Insulators are notoriously poor conductors of electricity.
If the headlights seem dim, if there are nagging and intermittent electrical problems, if the vehicle is old and if inspections similar to those mentioned to this point fail to resolve the problem(s), there is a high probability that oxidation is the cause. Even a cursory inspection will reveal that almost all the terminals at the ends of the wires in the wiring harness (regardless of the make of the car or country of origin) are crimped, not soldered. Regardless of how firmly the crimp was made when the terminal was attached to the wire (perhaps 20 years ago - more in some cases), oxygen will get to the crimped connection. The oxygen will combine with the copper to form insulating copper oxide, and over the years this oxide will constantly decrease the efficiency of current flow between the terminal and the wire to which the terminal is crimped.
A temporary solution is to wash the connections liberally with TV tuner cleaner and re-crimp the terminals. Note: this is only a temporary solution! For a permanent fix there are basically two choices: one, cut each offending terminal from the harness and solder a new terminal in its place; or two, replace the complete wiring harness.
Vintage sports cars are passionately loved by their owners and drivers. A special breed of enthusiast keeps these cars on the road in safe driving condition. Once the challenge to preserve these treasures is accepted, it is in the best interest of all concerned to share information. The intent of this presentation is to disseminate practical information among those who love these vehicles and work to keep them rolling, insuring that future generations will have the opportunity to enjoy and appreciate them as much as we do.
Back to General Tech Tips
|
|