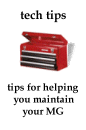

Chicagoland MG Club
General Tips
MGA Tips
MGB Tips
Midget Tips
MGT Tips
MMM Tips
Tech Session Photo Archives
|
|

Your Ignition System - Back to the Basics
This is the first of a series of articles on basic tuning techniques to help you maintain your car to original factory specifications. Since the ignition system must be in good order before any other systems, such as the carburetor(s), can be properly adjusted, we will begin with a brief discussion on ignition timing procedures. These instructions assume that the ignition system components (wires, spark plugs, distributor and its parts) are in good workable condition.
Ignition Timing
Ignition timing refers to the point during the combustion cycle at which the spark plugs fire, and is expressed in degrees of crankshaft rotation in relation to the top dead center (T.D.C.) position of the pistons. Specifications for timing include the number of degrees before or after top dead center, and the required engine speed at which the setting must be made. Supplemental instructions such as "disconnect vacuum advance line" may also be given. When a specific engine speed (other than "static") is given, or for electronic ignition systems, timing must be done using a stroboscopic timing light. For most of our older British sports cars, however, "static" timing is specified. This simply means that the timing is set with the engine not running.
Before considering checking or setting the ignition timing, it is imperative that the condition of the points and the point gap be checked and reset, if required. While most Lucas point type distributors require a point gap of .014" to .016", check your workshop manual for your particular distributor's requirement. Adjusting the point gap is really an indirect way of setting what is known as the dwell angle. This is the angular period of rotation of the distributor cam during which the points remain closed. Setting the point gap with the aid of an inexpensive dwell meter is much more accurate than setting with a feeler gauge. Do not neglect this setting - the dwell angle is one of the most important settings on a car, having serious effects on performance and fuel economy.
All engines have some sort of timing mark - one or more marks on the crankshaft pulley or fly-wheel, which align with a fixed mark on the timing chain cover or engine block. A pair of these marks will align when the piston in the "timing cylinder" (usually No. 1 cylinder) is at top dead center. Consult the appropriate workshop manual for information specific to your engine. Occasionally, the timing mark or pointer may be missing or improperly positioned. (This is fairly common on TR2-4A, where the crankshaft pulley is easily installed with the timing mark in the wrong position in relation to the crankshaft throws.) When these conditions exist, top dead center may be found by removing the appropriate spark plug and observing the piston movement through the spark plug hole while turning the engine over by hand. When the piston reaches its highest position, it is at top dead center. When you are satisfied that top dead center has been accurately located, mark the position for future reference.
The static timing procedure is not difficult. The only equipment required is a 12-volt test light. If a commercial test light is not available, a substitute may be easily made by soldering two wires to a 12-volt light bulb; one wire to the side of the base, and the other to the bottom contact. For convenience, alligator clips may be installed on the other ends of the wires.
To static time your engine:
1) As accurately as possible, locate the piston of the "timing cylinder" at top dead center, on the compression stroke. This is achieved by noting the position of the ignition rotor when the piston is at top dead center. If the rotor points to the contact on the distributor cap which leads to the spark plug of the "timing cylinder", the piston is on the compression stroke. If the rotor points away from that contact, the piston is on the exhaust stroke, and the crankshaft must be rotated one full turn to bring the piston to top dead center on the compression stoke. Check that the timing marks line up correctly. (If the distributor has been removed from the engine, consult an appropriate workshop manual for proper re-installation instructions.)
2) If your vacuum advance unit has an adjuster, you may either proceed with the instructions in this paragraph, or skip it and go to paragraph 3, continuing from there.
If your pulley or indicator is marked with degree settings, turn the crankshaft until the single mark and the appropriate degree mark line up. If your pulley or indicator is not marked in degrees, use a timing degree wheel (Moss # 384-910) to set the crankshaft to the proper advanced or retarded setting as specified for your engine. It is essential that a reliable workshop manual be consulted for this specification. The piston of your "timing cylinder" is now in the correct firing position, and the distributor must now be adjusted to is firing position.
3) Loosen the distributor clamp to the point where the distributor may be rotated freely. Set the adjuster on the vacuum advance unit (if present) to mid-scale.
4) Connect one wire of the test light to the low tension contact on the distributor, and the other wire to a good ground. (The low tension contact is where the thin wire from one side of the ignition coil connects to the distributor.)
5) With the ignition on (but the engine not running), rotate the distributor body slowly in the opposite direction of the rotor's rotation until the test light lights up, indicating that the points have just opened. Do this a few times until you have accurately determined the exact point at which this happens, and re-tighten the distributor clamp bolt.
6) For distributors with adjusters on the vacuum advance unit, only if paragraph #2 was skipped:
With the piston of the "timing cylinder" at top dead center (see 1.), the adjuster on the vacuum advance unit may be used to "dial in" the correct static advance setting. One division of the scale is equal to four degrees. Count the "clicks" on your adjuster nut between divisions, and divide by four for the number of clicks per degree (generally about ten per degree, but check your individual distributor). Multiply this by the number of degrees advance you require, and set accordingly. Refer to a reliable workshop manual for this setting. Be sure to turn the adjusting wheel in the direction of the "A" to advance, in the direction of the arrowed "R" to retard.
7) Disconnect the test light and start the engine. If it does not start, make sure that you remembered to replace the rotor after adjusting the points. Don't feel foolish if you find it on top of your battery or wiper motor - there probably isn't a single auto mechanic dead or alive who hasn't had this happen.
Back to General Tech Tips
|
|