The MGA With An Attitude
LAYSHAFT Hardness and Dimensions - GT-204A
Something trivial has been bugging me, and comes up fairly often on various BBS. Moss Motors part number 461-560 - LAYSHAFT, for laygear, MGA and early MGB gearbox. In the Moss MGB parts catalog it is noted as being 0.643 diameter. It is actually 16.4-mm maximum diameter (0.6456" max). Tolerance range can be 0.6455-0.6450, so it should be noted as 0.645 diameter rather than 0.643.
There have also been lots of prior notes about soft shafts with very high wear rate and very short life, sometimes less than 10,000 miles. A standard simple check is to run a file or hacksaw across the OD (in a non-bearing area). File should not mark the surface if it is properly hardened. Some people are sending the new layshafts out for additional surface hardening, which makes for a huge increase in cost of the shaft. So I put this question to Moss Motors with the following reply.
On 6/5/2010, Michael Grant from Moss Motors wrote:
"The layshaft we were buying back in 2005 was checked against an original layshaft and we determined that the hardness and dimensions were not as consistent as they should have been. We actually blocked sales from 7/19/05 to 8/24/05 while we found another supplier. We did find a source in the UK and we have been buying shafts from them since. The change in vendors raised our cost significantly and we raised our prices to compensate. We have the ability to "lock" purchasing to a single source to prevent filling in with what may be inferior product and we have done so.
John Twist returned a shaft in September 2007 that had been installed in a customer's car in December of 2006.
He felt the shaft was worn excessively, and John was sure the shaft came from us; but it is unclear exactly when it was purchased. We had that shaft tested when it came back and it was 24 HRC. Concerned, we checked our stock - new shafts pulled from stock 19-Sept-07 averaged 59 HRC. It is very likely that the failed shaft was from the pre-2005 source. Nevertheless, we will not take a chance with this layshaft.
This part is still inspected every time they come in. We measure the OD and the length (both overall and to the step) of every layshaft received. Any found to be too long are sent to our shop to be machined. A random sample are tested for hardness. The results are entered into a perpetual spreadsheet. As a result of the steps taken, we have a high degree of confidence in the shafts we are selling".
Addendum December 2012:
On 20 December 2012, Ed Bell in Oregon, USA wrote:
"I have my transmission apart due to a failure of the new caged layshaft bearing that I installed about 15,000 miles ago. I have obtained a NOS bearing from a local source but am having trouble getting a new layshaft. The first one I purchased from a local Moss distributor was soft. He called Moss and was assured that all of their shafts were correct and Rockwelled at 52/53 RC. That is soft enough that a file easily removes material. (I think they have left off the case hardening process). My old shaft is hard enough that a file will not mark it at all. After rejecting two more soft shafts sent from Moss in Los Angles I purchased one from Brown and Gammons in the UK. It arrived today and is properly heat treated but the diameter is 0.642 and my old one is 0.645. It is a very loose fit in the holes in the case. Can I use it or is that too small"?
It is to small for proper mating with the roller bearings. The shaft should be 0.6455-0.6450 diameter, serving as the inner race for 16.4mm roller bearings. When it is 0.003 too small it will cause excessive loading on a few rollers of the bearing, and accelerated wear on the shaft. If the super hard rollers survive (which they usually do), the shaft will eventually wear down a couple thou on the lead bearing side until it conforms to the working diameter of the roller bearing. This then causes a misalignment of the rotational axis of the laygear, in which case you may get an audible whine from the gear teeth under working load in the lower gears.
The shaft may be high carbon steel, possibly heat treated followed by case hardening. Case hardening of the shaft is only a few thousandths of an inch deep. Once it wears through the hard surface the wear rate will accelerate, and end of life is near at hand. I would not install the undersize shaft.
Addendum April 2013:
In March 2013, Lee Simmonds reported receiving a "soft" layshaft from Scarborough Faire. S.F, claims they sourced that particular part from Moss Motors. Moss agrees they did sell two pieces to S.F. in November 2012 (but no telling for sure if it is the same part). Lee Simmonds commissioned a professional shop to hardness test the parts. The original layshaft removed from his worn gearbox tested hardness at 60 RC. The replacement part tested 50 RC. The part with 50 RC hardness can be scratched with a file or hacksaw blade, while the 60 RC part cannot be scratched.
On April 4, 2013, Blaine Graham at Moss Motors reports:
"I asked that five of these, at random, be pulled from stock here and tested for hardness. This was done right away. The HRC results were 49.5, 48, 49, 49, 48. The target is 50. Hitting within two points of the target is well within specifications. The one John Twist used in his video six years ago was returned to us. It tested to have a hardness of HRC 24. That was clearly unhardened".
So there is "hard", and there is "bearing hard". RC 24 is definitely soft, not hardened. RC 49 is hardened, but not as hard as would be desired (or required). A quick search of bearing suppliers yields a consensus that a shaft to be used as inner race for a roller bearing should be RC 60 minimum surface hardness. While the Rockwell "C" scale for hardness is roughly linear, wear resistance is not linear. A relatively small change of hardness results in a relatively large change in wear characteristics. 50% increase in hardness can yield 50X increase in shaft life. Roughly speaking, the difference between RC 49 and RC 60 could yield 20X increase in wear resistance. When you invert the fraction, the difference between RC 60 and RC 49 could yield a 95% reduction of wear life (roughly speaking). Therefore, as a roller bearing shaft is concerned, RC 49 may be "hardened" but is not hard enough. When the shaft can be scratched with a file or hacksaw blade, it is not RC 60 hardness.
Blaine Graham at Moss further reports:
"When this matter came up six years ago, we set an inspection flag for these. At the time, we pulled random samples and had them tested by an outside company. When a reasonable number of orders passed muster with no issues, we stopped the random testing. .... We test every one for dimensional compliance, but not for hardness. We will not test for hardness again unless we have a reason to, as we did today".
From notes farther up the page, in 2011 Moss was supplying parts that were RC 59. Now we have the case where Moss Motors is knowingly selling parts with RC 48 to 53 hardness thinking they are suitable as roller bearing shafts (which they are not), and they are no longer testing hardness for each new supply order. I will drop another note to Moss to see what can be done.
See also Faulty Parts article FT-050
Addendum, Jan 22, 2015:
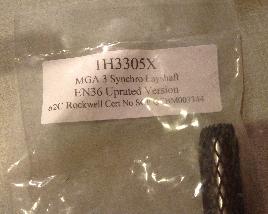
After a few fits and starts, a couple of rejects and re-manufacture, Moss Motors UK now has new layshafts advertised as 60-62 HRC. You must order part number 1H3305X, as the softer shafts are still being sold under the original part number 1H3305. Hopefully these will be available soon from Moss Motors USA.
|