(Continued from page 8)
3. |
Suitable wiring
Finally, make sure that the wires you are using have the correct current capacity for the power they have to take. Using cable that is too thin is the electrical equivalent of reducing three lanes of motor way into one - total breakdown - if the current is much higher than the wire, the wire will act like a fuse and melt.
|
Making Connections
|
1. |
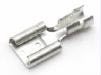
Spade connectors
Strip back 1/4" of wire without ripping out half of the strands, (if you have never used wire strippers before, have plenty of practice with some old bits of wire) twist the strands together and solder the bare end.
Always heat the wire with the soldering iron and apply the solder to the wire while it is still in contact with the iron. The wire must be hot enough for the solder to flow into the wire strands - but don’t keep the iron there for too long, otherwise the outer sleeve of the wire will melt back. It is an art worth learning.
Do not apply solder to the iron and then try to "blob" the solder on to the wire - it never works because the solder "dries out" as the flux evaporates, and then the resulting joint can become brittle and prone to breaking (aka "Dry Joint").
Once cool, fit a spade connector sheath over the wire and then crimp the connector to the wire as shown in the diagram The crimping makes a mechanically sound connection, but this is not enough. Returning to the soldering iron, you then need to apply heat to solder the wire to the connector to ensure an enduring connection, just like they do at the factory.
|
2. |
Bullet connectors

Bullet connectors are needed where (A) two separate lengths of wire are to be joined together or (B) where an extra wire is to be added to a main feed.
Many bullet connectors can be crimped on as well as soldered to enhance the quality of their connection, but the stock items used by BL tend to be a bit more tricky and can only be soldered - so you must ensure that the soldered connection is not dry!
Strip back 3/8" of cable and solder the strands. Insert in the end of the bullet - it may help to "kink" the strands slightly to keep the bullet in place - and then re-apply the soldering iron to the top of the bullet. Allow it to heat up and then apply the solder through the hole at the top of the bullet so that it can run inside, attaching the cable to the wall of the connector.
The advantage of these connectors is that, if corroded, the connector block can be thrown away and a new one fitted without having to do any more soldering. Also, they can provide multiple outlets for power, but watch out for that current overload on the original feed wire!
The disadvantage is that the connector is a mechanical fit and prone to electrical failure when corroded, which is why many cars start going wrong after five year’s use!
|
| | |
An Extra Fuse Box
If you are accessory mad, the use of a fuse box with a direct link to the solenoid may provide a safe, efficient answer, rather than connecting countless new wires onto an overburdened wire feed.
Again, make sure that the wire, from the feed to the box has sufficient capacity to deal with any load place upon it (an in-line fuse may further protect the entire system).
Is it worth the effort you might ask? Yes! A clean job is a good job!
|
|
1. |
If it’s soldered, then the connections will be better, stopping niggling electrical failures and dangerous burn-outs; the connectors are cheaper too. |
2. |
The proper connectors often allow easier access for repair of equipment. |
3. |
Stops wires from sparking and equipment lasts longer. |
4. |
It looks better, too! |
Reprinted from the MG Experience website — Moss Motors MGB Tech Tips
|