
Chicagoland MG Club
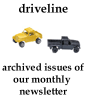
Back to Archives
Submit an article
Cover
Intro & Club Officers
The Steering Column
The Passenger Seat
August Meeting Report
Welcome New Members
The Rallye Corner
Lucas Night Rally
Christmas Already?
Import Night, Downers
Abingdon Summer Party
Cut & Weld Tech Day
Donald M. Healey Rally
BCU All British Social
BCU British Car Festival
Family Go-Kart Night
Siemens Autocross
Regalia Items Available
Regalia Order Form
"Maynard's Surprise"
Fall Color Tour
Halloween Rally
True Story
Just a Simple Wrench
MG/Lola In Hillclimb
Scratched Windshields
Classifieds
CMGC Events
Other Events
Back Cover
|
|

Cut & Weld Tech Day
August 24, 2002 - Glen Ellyn, IL
With our gracious hosts
Jim and Lois Evans

At least 14 people were in attendance for Cut and Weld Tech Day at the Evans home in Glen Ellyn. The subject of attention was a moderately rusty (said with tongue in cheek) 1977 MGB needing recycling, and in the process we all got some hands on experience with the BIG BOY TOOLS. Most of the disassembly work was done first, and it didn’t take long to haul out the air wrenches, the cutting torch, the BIG hammers and even BIGGER crowbar and the Sawzall. Ohhh-ho-ho! Bring on the Power, and then MORE POWER. Ahrrrrrr! Would have made a grand new episode for Tim Taylor and Tool Time. With all the willing hands and the power tools it didn’t take long to strip and gut the car, and lots of good used parts were finding new homes.
Then came the other half of the reason for being there, trying out the Plasma Cutter and the MIG welder. These tools are all portable, and they do all run on 120 volt power outlets, but you should maybe be careful what you plug in where. With the air compressor and the plasma cutter going at the same time we did manage to blow a couple of house fuses. Apparently tha plasma cutter draws a significant momentary surge of current when you strike the arc, similar to the start up surge of a large electric motor. It took a little while to figure out that the spring loaded nozzle of the plasma cutter torch contains a small switch that actuates a high frequency starting current. Press the trigger to start the air flow and turn on the power, then just give the nozzle a little bump on the work surface to strike the flame, and it works perfectly every time.
Fuel for the plasma cutter is just wall power electricity and compressed air at about 80 psi. The air shoots out of a small nozzle in a stream about the size of a pencil lead. The torch uses electric current to heat the air jet hot enough to ionize the molecules to create a plasma, and the plasma jet burns through sheet metal quickly and easily. Beyond that the practice is primarily to hold a steady hand to make a straight cut, and it can help a lot if you can use a straight edge to guide the torch. Using a ridge in the car body for a guide, tilting the torch tip a bit forward in the direction of travel, and running the plasma torch steadily along at about one inch per second can produce a very narrow cutting kerf in the sheet metal panel with an finished edge that can be so smooth that it might feel like it was painted when you run a finger along it. And under the right conditions, if you don’t dawdle, the heat is so localized that it hardly affects the paint along the edge of the kerf. On the other hand, if you try to free hand a cut without a guide you can end up with a reasonable faimile of saw teeth.. And if you go a little too slow it will blister the paint within about 1/4 inch of the cut. But the plasma cutter uses a whole lot less heat than an acetylene torch, will almost never distort the panel, ang is a lot faster than using a saw or an acetylene cutting torch. It is indeed a sweet tool for cutting sheet metal.
Lots of people were also practicing a bit with the MIG welder and tacking sheet metal parts together. This too is easy with just a little practice. Shielding gas flows out of the torch nozzle and against the work surface surrounding the weld zone, and a small wire is pushed out with an automatic feeder into the weld some as required. Again the practice is primarily for using a steady hand to keep the weld as smooth as possible.
Jim gave is one final demonstration of a nifty use for the MIG welder while repairing a torn out wend nut in the car body. Place a hex nut on a large flat washer and tack weld those two parts together. Drill about four small holes in the body panel around the torn out hole in the body panel. Position the new weld nut and wesher part behind the panel in place of the original captive nut. Then use the MIG welder to plug wend through the drill holes in the panel to attach the new paart to the panel. Grind the welds smooth, and the panel has new captive threads good as new and ready to paint.
See more photos and notes at:
www.chicagolandmgclub/photos/cut_weld
|
|